Stranggießen

Stranggießen ist ein kontinuierliches Gießverfahren zum Herstellen von Halbzeug aus Eisen- und Nichteisenlegierungen. Beim Stranggießen wird das Metall durch eine gekühlte bodenlose Kokille gegossen und mit erstarrter Schale und meist noch flüssigem Kern nach unten, seitwärts oder oben abgezogen. Nach dem Durcherstarren wird der Strang geteilt.
Das Stranggießen ist nicht zu verwechseln mit dem Strangpressen, mit welchem Vollprofile und Hohlkammerprofile etwa aus Aluminium, Kunststoff (siehe Extrusion) und Keramik erzeugt werden.
Technik
[Bearbeiten | Quelltext bearbeiten]Nach der Kokillenanordnung wird zwischen horizontalem und vertikalem Stranggießen unterschieden. Horizontales Stranggießen wird aber überwiegend[1] für Nichteisenmetalle angewendet. Vertikale Stranggießanlagen mit gebogener Kokille gießen ein vorgebogenes Halbzeug, um es horizontal abziehen zu können. Das Halbzeug muss dann nach dem Erreichen der Horizontalen, vor dem Trennen, gerichtet werden. Mit vertikalen Kokillen ist entweder die Länge vom Gussstück durch die Anlagenhöhe begrenzt, oder der Strang muss mit noch flüssigem Kern gebogen und nach Erreichen der Horizontalen wieder gerichtet werden.
Für den bei Nichteisenmetallen vorwiegend angewandten vertikalen Strangguss, wird eine unten offene, wassergekühlte Kupferkokille verwendet, auch Kragenkokille genannt. Flüssigmetall wird ihr über ein Verteilersystem, kontinuierlich bei dosierter Gießgeschwindigkeit zugeführt. In einfachster Form steht hierbei zwischen Schmelzofen und Kokille ein Eingusstiegel, auch Tundish genannt. Innerhalb der Kokille bildet sich eine Strangschale, die den anfangs noch flüssigen Kern umschließt. Der aus der Kokille austretende Strang wird in ein die weitere Abkühlung begünstigendes Becken abgesenkt und dabei ständig mit Wasser besprüht. Beim diskontinuierlichen Verfahren begrenzt die Tiefe dieses Abkühlbeckens die Länge der Knüppel, Barren oder Ronden.
Stranggussanlagen werden ein-, zwei- oder mehrsträngig gebaut. Je kleiner die Querschnitte sind, desto mehr Stränge werden benötigt, um den Kapazitäten der vorgeschalteten Aggregate gerecht zu werden. Besonders beim Gießen von Rundbarren (auch Ronden oder Pressbolzen genannt) kommen dagegen Kokillensysteme zum Einsatz, die es ermöglichen, bis zu 32 Ronden mit Durchmessern im Bereich von 120–150 mm gleichzeitig zu gießen.
Die Technik des Stranggießens unterscheidet sich nur wenig, ob nun Stähle, Kupferlegierungen oder Aluminium verarbeitet werden. Der wesentliche Unterschied liegt bei den Temperaturen, die von ca. 700 °C bei reinem oder legiertem Aluminium bis >1600 °C bei Stahl reichen. Versuche, kontinuierlich zu gießen, reichen in die Mitte des 19. Jahrhunderts zurück. Entscheidende Fortschritte wurden ab 1930 erzielt (Junghans-Rossi-Verfahren für Leicht- und Schwermetalle).
Im Gegensatz zum individuell geformte Gussstücke hervorbringenden Kokillenguss ist Strangguss ein semikontinuierliches bis kontinuierliches Verfahren. Bei semikontinuierlich arbeitenden Anlagen bestimmt deren Bauhöhe die maximale Länge des jeweiligen Stranggussprodukts. Kontinuierliche Arbeit bedeutet Gießen eines Endlosstranges. Dieser kann entweder durch eine Säge („fliegende Säge“) unterteilt werden, sobald ein Strangabschnitt ausreichend erstarrt ist, oder der Strang wird zum Bogen umgelenkt und verlässt die Anlage als horizontaler Strang. Diese Technik wird unter anderem bei der Herstellung von Stranggussmasseln für Formgießereien, oder bei der Verarbeitung von Kupferwerkstoffen zu Stangenmaterial oder Rohren verwendet. Auch bei Strangguss aus Kupferlegierungen[2] wird sowohl horizontal als auch vertikal gegossen.
Halbzeug werden die Stranggussprodukte deshalb genannt, weil sie sich bis zum Endprodukt noch weiteren Bearbeitungsgängen unterziehen müssen. Walzen, Pressen und Tiefziehen kommen mehrheitlich zur Anwendung, verbunden mit einer vorausgehenden zeitlich terminierten Auslagerung bei Raum- bzw. Umgebungstemperatur, oder einer vor- bzw. nachgeschalteten thermischen Behandlung (Anlassen und Auslagern).
Stranggießen von Stahl
[Bearbeiten | Quelltext bearbeiten]Spezielle Technik
[Bearbeiten | Quelltext bearbeiten]
Eine Stranggießanlage besteht aus[3]
- dem Pfannendrehturm zum Einsetzen der Stahlgießpfanne,
- dem Verteiler (engl. tundish), der die Schmelze zur Kokille leitet,
- der Kokille mit der Schmelze (Primärkühlbereich),
- Tauchrohr und Schattenrohr
- Schieferplatte zur Regulation des flüssigen Stahls
- der Kokillenoszillations- und -haltevorrichtung,
- dem Strangführungssystem (Gießbogen) mit Sekundärkühlung,
- den Treib- und Richtapparaten,
- dem Auslaufrollgang,
- der Querteilanlage (Brennschneidanlage, Schere),
- der Markiermaschine (Signierung) und
- dem Kaltstrang.
Die Schmelze wird gewöhnlich mit einer so genannten Fähre vom Schmelzaggregat über den Gießkran zur Stranggießanlage transportiert und im Pfannendrehturm eingesetzt. Über einen Bodenablass (Ausguss), der durch einen Schieber verschlossen wird, fließt die Schmelze in den Verteiler. Damit der flüssige Stahl nicht mit dem Luftsauerstoff reagiert, wird der flüssige Stahl dabei in einem Schattenrohr geführt bzw. mit Gießpulver bedeckt. Der Verteiler erfüllt zunächst die Funktion eines Puffergefäßes, damit es während eines Pfannenwechsels zu keiner Unterbrechung des Stranggussprozesses kommt. Zusätzlich hat der Verteiler bei Mehrstranganlagen die Funktion, den Flüssigstahl auf die einzelnen Stränge zu verteilen. Die Schmelze wird im Verteiler durch eine Schlackeschicht (meist Reisschalenasche) abgedeckt.
Aus dem Verteiler läuft die Schmelze frei oder durch ein Tauchrohr (auch Gießrohr genannt) in die Kokille. Der Durchfluss wird in Abhängigkeit vom Gießspiegel in der Kokille mit einem Stopfen oder einem Schieber gesteuert. Um Anbackungen am Verteilerausguss durch Tonerde (Al2O3) zu vermeiden, wird teilweise mit Argon gespült und die Schmelze kann elektromagnetisch gebremst oder gerührt werden, um die Strömung des Flüssigstahls zu beeinflussen. Der Gießspiegel in der Kokille wird mit Schlacke abgedeckt. Diese verhindert Reoxidation der Schmelze, bindet aufgestiegene Unreinheiten und dient als Schmiermittel zwischen der erstarrten Schale und der Kokille. Zum Bilden der Schlacke wird kontinuierlich Gießpulver auf den Gießspiegel aufgebracht. Während des Gießens wird die Kokille oszillierend bewegt, um ein Anbacken des Stahls an den gekühlten Wänden der Kokille (z. B. Kupfer- und Nickelplatten) zu verhindern und den Transportvorgang zu unterstützen. Beim Verlassen der Kokille hat der Strang eine erstarrte Schale von wenigen Zentimeter Dicke, während der Großteil des Querschnitts noch flüssig ist. Unterhalb der Kokille wird der Strang im sogenannten Gießbogen (Kreiszone Radius 10 m) von außen durch Luft-/Wasserbesprühung (sekundär) gekühlt. Außerdem wird er durch Rollen gestützt, um das Ausmaß des Ausbauchens zu verringern, das wegen des auf die Strangschale wirkenden ferrostatischen Druckes erfolgt. Diese Strangführungsrollen, die höchsten Beanspruchungen ausgesetzt sind, gehören wegen ihres Einflusses auf die Strangoberfläche zu den zentralen Bauteilen einer Stranggießanlage. Aus diesem Grund werden die Rollen mit einer korrosions- und verschleißbeständigen Schicht versehen, die früher aufgeschweißt wurde. Heute werden diese Rollen immer häufiger als „Verbundguss“ im Schleudergussverfahren hergestellt.
Stahl hat im Vergleich zu anderen Metallen wie Aluminium oder Kupfer eine relativ niedrige Wärmeleitfähigkeit. Dadurch ergibt sich eine große Stranglänge von bis zu 20 m vom Gießspiegel bis zum völligen Erstarren der Schmelze (sog. „metallurgische Länge“). Erst nach der Durcherstarrung kann der Strang in einzelne Brammen geschnitten werden. Anlagen, bei denen die Stränge nach dem Verlassen der Kokille senkrecht weitergeführt werden, erfordern daher eine große Bauhöhe und werden nur selten eingesetzt. Bei den meisten Anlagen wird der Strang in einem Radius (je nach Strangdicke) von etwa 7 bis 15 m gebogen, bis er beim Erreichen eines horizontalen Winkels mit einer Biege- und Richteinheit wieder gerade gerichtet wird. Die Kokille kann dabei entweder gerade oder gebogen ausgeführt werden. In geraden Kokillen verlässt der Strang die Kokille senkrecht nach unten und wird erst durch die anschließende Walzenführung gebogen, in gebogenen Kokillen ist der Strang bereits kreisbogenförmig. Beide Konzepte haben ihre spezifischen Vor- und Nachteile, die daraus resultieren, dass einerseits durch das Biegen des Strangs Risse entstehen und andererseits eine lange vertikale flüssige Strecke Vorteile für die Reinheit des Stahles bietet, da Unreinheiten in die Schlacke aufsteigen können. Nach dem Durcherstarren wird der Strang auf dem Auslaufrollgang mit Brennern in Längen geschnitten.
Für das Angießen wird ein Anfahrstrang (Kaltstrang) von unten oder oben in die Kokille eingeführt, der die Unterseite verschließt. Der eingefüllte Stahl erstarrt auf dem Anfahrstrang und wird mit diesem nach unten abgezogen. Nach Erreichen der metallurgischen Länge werden der Anfahrstrang und der Gussstrang voneinander getrennt (entkuppelt).
Verfahrensarten nach dem Endprodukt
[Bearbeiten | Quelltext bearbeiten]
Beim Stranggießen unterscheidet man mehrere Verfahren, die vom Format des zu gießenden Stranges abhängig sind:
- Im Knüppel- und Vorblockstrangguss werden runde oder annähernd quadratische Querschnitte (Knüppel) oder sogar profilförmige Querschnitte vergossen. Sie dienen zur Herstellung von Stangen, Drähten und Profilen.
- Im Brammenstrangguss werden Brammen, also rechteckige Stränge mit großer Breite (bis über 2600 mm) und kleiner Dicke (bis 600 mm) zur Blechherstellung erzeugt. Beim Brammenstrangguss unterscheidet man weiter:
- Brammenstrangguss allgemein (Dicke über 100 mm bis 600 mm)
- Vorbrammenguss oder (Dicke von 70 bis 300 mm)
- Dünnbrammenguss (Dicke von 40 bis 100 mm)
- Vorbandgießen (Dicke von 15 bis 50 mm[4])
- Bandgießen (Dicke wenige mm).
Bei den beiden letztgenannten Verfahren sind erhebliche Einsparungen im Bereich der Anlagentechnik und der Energiebilanz möglich. Eine weitere Reduktion der Umformprozesse wird durch das Dünnbandgießen (siehe dort) erreicht.
Vorbandgießen
[Bearbeiten | Quelltext bearbeiten]Durch das Vorbandgießen wird eine Dünnbramme mit etwa 50 mm Dicke erzeugt, die direkt in der Fertigungsstraße eines Warmwalzwerkes angestochen werden kann. Zwischen der Gießmaschine und dem Walzaggregat wird nur noch ein Ausgleichsofen benötigt. Mit diesem Verfahren können kostengünstig viele Stahlqualitäten verarbeitet werden. Nachteile sind geringe Flexibilität und Oberflächenqualität der Bänder.
Bandgießen
[Bearbeiten | Quelltext bearbeiten]Bandgießen ist ein kontinuierliches Gießverfahren, mit dem Metallbänder hergestellt, die anschließend nicht oder nur in wenigen Stichen (Durchlaufen durch ein Walzgerüst) umgeformt werden. Das Verfahren wird vor allem für Nichteisenmetalle verwendet.
Das 2-Rollen-Bandgießen von Stahl wurde bereits im 19. Jahrhundert durch Henry Bessemer patentiert. Er konnte es allerdings nicht in die Marktreife überführen. Erst nach 1990 wird es für rostfreie Stähle und Elektrostähle industriell genutzt. Hier erstarrt der Stahl zwischen zwei sich gegeneinander drehenden wassergekühlten Walzen und wird vollständig erstarrt als Band, mit max. 6 mm Dicke[5], nach unten abgeführt. Die Geschwindigkeit der Gießwalzen muss genau auf die Gießtemperatur abgestimmt sein, da es bei nicht vollständiger Erstarrung (zu hohe Gießtemperatur und/oder Walzengeschwindigkeit) zum Durchbruch kommt. Ist die Schmelze jedoch zu früh durcherstarrt, sind die Kräfte an den Walzen zu groß und kann sogar den Prozess lahmlegen (zu geringe Gießtemperatur und/oder Walzengeschwindigkeit).
In die Anlage wird typischerweise ein Walzgerüst eingeordnet, in dem (bei geringer Gießdicke) nach einem einzigen Walzstich bereits eine Banddicke von 1 mm – zugleich das mögliche Minimum – ergibt. Das gewalzte Dünnband wird wassergekühlt und auf Rollen, sogenannte „Coils“ aufgewickelt.
Das Verfahren bietet den Vorteil des geringen Investitionsbedarfs sowie die Möglichkeit auch kleinere Lose kostengünstig herzustellen. Da zudem die für das Auswalzen von Brammen erforderliche Wiedererwärmung entfällt, ergeben sich weitere Ersparnisse bei den Kostenfaktoren Zeit und Energie.
Stranggießen von Aluminium
[Bearbeiten | Quelltext bearbeiten]Spezielle Technik
[Bearbeiten | Quelltext bearbeiten]Das Stranggießen von Aluminium, auch unter der Oberbezeichnung Formateguss einzuordnen, kann wie auch bei anderen Metallen als diskontinuierlicher oder kontinuierlicher Prozess erfolgen. Im ersteren Falle werden Barren oder Ronden von durch die Anlage vorgegebener Länge hergestellt. Im anderen Fall wird der gegossene Strang nach Erreichen der gewünschten Länge von einer synchron mitgeführten Säge („fliegende Säge“) zerteilt – ohne Unterbrechung des Gießvorgangs.
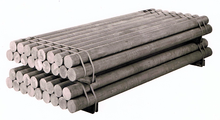
Unabhängig von solcher anlagebedingten Unterscheidung wird das flüssige Aluminium über einen Eingusstiegel oder über eine Gießrinne und ein dieser nachgeordnetes Verteilersystem der Kokille zugeführt. In der Gießrinne können Legierungszusätze – in Abhängigkeit von der Gießgeschwindigkeit automatisch dosiert – zugefügt werden. Meist sind es Titan und Bor enthaltende Vorlegierungen zur Gefügebeeinflussung (Kornfeinungsmittel).
Der Strang erstarrt in der wassergekühlten Kokille (Primärkühlung) rasch äußerlich und wird zur weiteren Abkühlung und Verfestigung in ein Kühlbecken (Sekundärkühlung) abgezogen. Absenkung und Zufluss in der Kokille erfolgen dabei im Gleichtakt. Die Gieß- oder Absenkgeschwindigkeit wird durch die vergossene Legierung bestimmt. Sie liegt im Mittel zwischen 5 und 15 cm/min.
Unterschiedliche Erstarrungsgeschwindigkeiten von Metallschmelzen werden stets im Gussgefüge sichtbar. Auf Grund der im Vergleich etwa zu Sandguss sehr schnellen, durch die Wasserkühlung bedingten Erstarrung gibt es keine Phasenausscheidungen. Bei bei Spektralanalyse von Strangquerschnitten findet im Normalfall keine Unterschiede der Zusammensetzung. Der rasche Wärmeentzug beim Stranggießen kann jedoch Spannungen innerhalb des Erstarrungsgefüges erzeugen, die beim Verwalzen zu Rissbildung führen können. Kaltauslagerung oder Warmbehandlung (Lösungsglühen) beseitigen solche Spannungen. Seigerungsartige Ausschwitzungen in der Gusshaut werden vor der Weiterverarbeitung abgefräst.
Um gießtechnische Fehler zu begrenzen, muss der legierungsabhängige Schrumpfspalt zwischen erstarrendem Metall und Kokillenwand möglichst klein gehalten werden, da Luft die Wärmeabfuhr behindert.[6] Ein weitaus größeres Problem als der Schrumpfspalt ist beim Stranggießen von Aluminium und seinen Legierungen die Empfindlichkeit des Flüssigmetalls im Hinblick auf Wasserstoffaufnahme und Oxidbildung, die jeweils eine besondere Behandlung der Schmelzen verlangen.
Schmelzebehandlung bei Strangguss
[Bearbeiten | Quelltext bearbeiten]Das Problem der Wasserstoffaufnahme, Vermeidung und Entfernung
[Bearbeiten | Quelltext bearbeiten]Wird der Strangguss in einer Gießerei hergestellt, die einer Primärhütte nachgeordnet ist spricht man international fachsprachlich von einem Cast-House. Diesem wird nur zuvor einer Schmelzebehandlung unterzogenes Metall angeliefert. Dabei kann es sich um Reinaluminium oder hüttenseitig bereits legiertes Materal handeln. Die Behandlung erfolgt die in einem Mixer oder auch Warmhalteofen und hat in erster Linie das Ziel, die Schmelze von aus der Elektrolyse kommenden Verunreinigen zu befreien. Das bedeutet eine weitgehende Reduzierung des Gehalts an Natrium und Calcium. Die Entfernung eines immer gegebenen Wasserstoffgehaltes nimmt man an spätestmöglicher Stelle vor. Vor dem Jahr 2000 war die Chlorierung mittels Chlorgas oder chlorabgebenden Zusätzen bevorzugt, da es die beiden Störelemente rasch in ihre Chloride überführte und diese zur Schlacke aufsteigen ließ. Überschüssiges Aluminiumchlorid brachte gleichzeitig eine nützliche Spülwirkung, da es bei gegebenen Temperaturen unter Aufwallung die Schmelze verlässt. Aus Umweltschutzgründen wurde die Verwendung von Chlor etwa ab 1980 zunehmend reduziert und Argon oder Freon mit allenfalls geringer Chlorbeimengung verwendet. Die Erfindung einer SNIF-Box genannt Behandlungskammer, die dem Verteilersystem unmittelbar vorgeschaltet wurde, ermöglichte feinere Dosierung und eine Entfernung des Wasserstoffs an letzter Stelle vor dem Vergießen. Dazu wird die Möglichkeit einer Wiederaufnahme aus feuchter Umgebungsluft begrenzt. Stand der Technik ist es auch, eine erforderliche Kornfeinung, bei gesteuerter Zuführung eines Drahtes, der mit feinenden Elementen legiert ist, unmittelbar vor die SNIF-Box zu legen. Die Entfernung der Oxide obliegt, sofern sie nicht bereits zuvor im Zuge der Behandlung ausgespült wurden, einer Filtration (siehe dort).
Recyclingbetriebe, die ebenfalls Stranggussmaterial aus Schrotten herstellen können, müssen speziell bei der Wasserstoffentfernung etwas mehr tun, da die eingeschmolzenen Schrotte oft korrodiert sind, also mit einer Hydroxidschicht behaftet, oder auch verölt sind. Auf Störelemente ist ebenfalls stärker zu achten, da das Recyclingmaterial zum Teil aus Formgießereien kommt, und zahlreiche unerwünschte Elemente enthalten kann. Nicht alle müssen oder können entfernt werden. Mit Magnesium- oder Kupfergehalten lässt sich stranggussgeeignetes Material bereitstellen, siliziumreiche Schmelzen eignen sich eher für die Herstellung von AlSi-Gusslegierungen.[7]
Das Problem der Oxidbildung, Vermeidung und Entfernung
[Bearbeiten | Quelltext bearbeiten]Bei gegebener Oxidationsneigung von Aluminiumschmelzen, besonders solcher mit Magnesiumgehalten ist es nötig, die Oxidation durch Anwendung sie hemmender Maßnahmen zu begrenzen (Schmelzebehandlung). In der Schmelze flottierende und in den Guss gelangende Oxide, meist Gamma-oxide in Form von Häutchen führen stets zu Gussfehlern. Auch bei Gießtechnik ist auf Schutz vor Oxidation zu achten. Sie kann bei Strangguss durch Umfüllvorgänge und dort im Gießstrahl erfolgen, aber auch im Verteilersystem. Eine nach Stand der Technik gute Sicherheit bietet die Filtration.
Schmelzefiltration
[Bearbeiten | Quelltext bearbeiten]Zur Herstellung von Aluminiumprodukten, an die besondere Qualitätsanforderungen gestellt werden, sei es bei Formateguss (Halbzeug) oder Formguss, müssen Oxideinschlüsse vermieden werden. Soweit eine Oxidation nicht vermieden werden kann, müssen die Schmelzen durch eine Spülung gereinigt werden. In der Vergangenheit wurde dies durch eine chlorierende Behandlung der Schmelze erzielt, also das Durchleiten von gasförmigem Chlor, sei es aus der Flasche, oder in situ freigesetzt. Die Chlorierung von Aluminiumschmelzen hat jedoch in heutiger Sicht verschiedene Nachteile. Unter anderem wird der Magnesiumgehalt der Schmelze verringert und insbesondere entstehen Probleme beim Umweltschutz, da das gebildete und bei Schmelztemperatur flüchtige Aluminiumchlorid teilweise in die Umwelt gelangen kann. Auch für die Arbeitsplatzhygiene ist der Umgang mit Chlor unerwünscht. Daher werden heute entweder inerte Gase oder Gemische mit geringen Chloranteilen verwendet.[8] Die entgasende und zugleich spülende, den Wasserstoffgehalt verringernde Behandlung, entfernt die gröberen und mit Wasserstoff behafteten Oxide. Sie kann durch eine zusätzliche Filtration, die auch Feinoxide erfasst, ergänzt werden.
Zwei Filtrierverfahren gelten als Stand der Technik: Anwendung entweder eines porigen Keramikfilters, oder eines von der Schmelze durchströmten Filterbettes, welches zumeist aus Petrolkoks besteht. Beide Verfahren sind geeignet, Oxide vor Eintritt der Schmelze in die Kokille abzufangen.
Ein nach seiner stofflichen Beschaffenheit als keramisch bezeichneter Filter für metallurgischen Gebrauch – nicht zu verwechseln mit auch in der Elektrotechnik eingesetzten Frequenzfiltern gleichen Namens – kann sowohl kreisrund, wie auch quadratisch sein und weist je nach Aufgabenstellung eine bestimmte Porenzahl je cm² auf. Er wird bei Strangguss möglichst nahe dem Verteilersystem der Stranggießanlage eingesetzt und erlaubt den Durchfluss einer bestimmten Metallmenge, bevor er ersetzt wird (Einmalfilter).
In eine Durchlauffiltration dieser Art kann noch ein Gasgegenstrom aus Argon oder trockenem Stickstoff eingebaut werden. Der Gehalt nach Behandlung sollte < 0,08 ml/100 g Aluminium sein.
Ein Vorteil der Filtration ist die mit der Oxidentfernung verbundene Reduzierung der Wiederaufnahme von Wasserstoff. In oxidhaltigen Schmelzen kann Wasserstoff aus feuchter Umgebungsluft sich nämlich über die Kontaktfläche Luft-Schmelze den vorhandenen Oxiden unter Bildung von Hydroxiden anlagern und zu Wasserstoffgehalten führen, die bei Messung weit oberhalb der Löslichkeitsgrenze liegen. Soweit ofentechnisch möglich ist daher besonders bei in Warmhalteöfen ruhenden Schmelzen ein Schutz der Badoberfläche mit geeigneten Salzgemischen angezeigt, alternativ mit einem Schutzgas, das schwerer als Luft ist.
Literatur
[Bearbeiten | Quelltext bearbeiten]- Schwerdtfeger: Metallurgie des Stranggießens. Stahl Eisen Verlag, Düsseldorf 1992, ISBN 3-514-00350-5.
- Aluminium-Taschenbuch. Band 1, 16. Auflage. Aluminium-Verlag, Düsseldorf 2002, ISBN 3-87017-274-6.
- Dieter Altenpohl: Aluminium von innen. 5. Auflage. Aluminium-Verlag, Düsseldorf 1994, ISBN 3-87017-235-5.
- Stephan Hasse (Hrsg.): Gießerei Lexikon. 17. Auflage. Verlag Schiele und Schön, Berlin, ISBN 3-7949-0606-3.
Weblinks
[Bearbeiten | Quelltext bearbeiten]- Überblick über die Stranggießverfahren von Nichteisenmetallen
- Schmelzebehandlung
- Metallurgie
- Stoff-Fluss: Schmelzen, Stranggießen, Wärmebehandlung, Schmieden
- Fotografien: Pfannendrehturm, Tundish (Verteiler), Strangführungssystem (Kreiszone)
Einzelnachweise
[Bearbeiten | Quelltext bearbeiten]- ↑ Schmelzen/Gießen – BGH Edelstahlwerke GmbH. Abgerufen am 16. September 2021.
- ↑ annähernd 90 % aller Kupferwerkstoffe werden im Stranggießverfahren kontinuierlich oder diskontinuierlich zu Halbzeug verarbeitet. s. Brunhuber, Ernst, Guss aus Kupferlegierungen, aus dem amerikanischen übersetzt, Verlag Schiele & Schön, Berlin 1986, ISBN 3-7949-0444-3.
- ↑ Die weltweit erste großtechnische Stranggussanlage für Stahl ging 1948 beim Breitenfelder Edelstahlwerk in der Steiermark in Betrieb.
- ↑ http://kerschgens.stahl-lexikon.de/index.php/stahllexikon/56-v/2802-Vorbandgie%C3%9Fen.html
- ↑ https://www.hindawi.com/archive/2016/1038950/
- ↑ Technische Anmerkung: Zur Reduzierung des Schrumpfspaltes sind im Zeitverlauf zahlreiche Maßnahmen vorgeschlagen worden, wie das Gießen mit möglichst niedrigem Metallstand in der Kokille. Eine andere Möglichkeit bietet der Einsatz konischer oder geriefter Kokillen. Eine geriefte Kokille bewirkt durch Lufteinschlüsse zwischen Kokillenwandung und flüssigem Metall zwar eine Verzögerung der Wärmeabfuhr, so dass bei gleich hohem Metallstand in der Kokille das Metall länger in Kontakt mit der Kühlfläche bleibt, aber auch die Kontraktion verschiebt sich damit weiter nach unten, der Schrumpfspalt wird kürzer. Das in der Sowjetunion erfundene, berührungslose Stranggießen in einem Magnetfeld wurde bereits in der zweiten Hälfte des 20. Jahrhunderts durch Alusuisse praxisreif, womit sich das Schrumpfspaltproblem weitgehend erledigte.
- ↑ Technische Anmerkung: Je größer der Wasserdampfdruck über der Oberfläche und je höher die Temperatur der Schmelze, umso höher ist der Wasserstoffgehalt, der sich als Gleichgewicht in der Schmelze einstellt. Der Einfluss der Temperatur auf die Gleichgewichtslöslichkeit des Wasserstoffs im Aluminium ist in Bild 1 wiedergegeben. Mögliche Wasserstoffgehalte von hochtemperierten Schmelzen sind in Bild 1 schraffiert eingezeichnet. Die Notwendigkeit solche Gehalte zu reduzieren liegt darin begründet, dass die Wasserstofflöslichkeit des Aluminiums nach Erstarrung auf weniger als 10 der Löslichkeit bei Liquidustemperatur fällt und der so entstandene Überschuss umso deutlicher als blasige Hohlräume im Guss zeigt, je langsamer die Erstarrung verläuft, also etwa bei Sandguss. Bei sehr rascher Erstarrung, wie sie bei Formguss in metallischen Dauerformen gegeben ist, verringert sich die Gefahr grobblasiger Ausscheidung, an ihre Stelle tritt Feinblasigkeit, oder Feinporosität. Der ursprünglich in der Schmelze gelöste Wasserstoff hat nicht genug Zeit um aus der rasch erstarrenden Gefüge Schmelze zu entweichen, was zur Folge hat, dass man im erstarrten Guss in aller Regel einen höheren Wasserstoffgehalt ermittelt, etwa mittels Dichteprobe, als im Gleichgewichtszustand löslich.
- ↑ Ein auf dieser Basis arbeitendes Gerät ist die Snif-Box, die eine Schmelzereinigung im „Durchlaufverfahren“ ermöglicht.