Eisen
Eigenschaften | |||||||||||||||||||||||||||||||||||||||||||||||||||||||||||||
---|---|---|---|---|---|---|---|---|---|---|---|---|---|---|---|---|---|---|---|---|---|---|---|---|---|---|---|---|---|---|---|---|---|---|---|---|---|---|---|---|---|---|---|---|---|---|---|---|---|---|---|---|---|---|---|---|---|---|---|---|---|
Allgemein | |||||||||||||||||||||||||||||||||||||||||||||||||||||||||||||
Name, Symbol, Ordnungszahl | Eisen, Fe, 26 | ||||||||||||||||||||||||||||||||||||||||||||||||||||||||||||
Elementkategorie | Übergangsmetalle | ||||||||||||||||||||||||||||||||||||||||||||||||||||||||||||
Gruppe, Periode, Block | 8, 4, d | ||||||||||||||||||||||||||||||||||||||||||||||||||||||||||||
Aussehen | metallisch glänzend mit einem gräulichen Farbton | ||||||||||||||||||||||||||||||||||||||||||||||||||||||||||||
CAS-Nummer | |||||||||||||||||||||||||||||||||||||||||||||||||||||||||||||
EG-Nummer | 231-096-4 | ||||||||||||||||||||||||||||||||||||||||||||||||||||||||||||
ECHA-InfoCard | 100.028.270 | ||||||||||||||||||||||||||||||||||||||||||||||||||||||||||||
Massenanteil an der Erdhülle | 4,7 % (4. Rang)[1] | ||||||||||||||||||||||||||||||||||||||||||||||||||||||||||||
Atomar[2] | |||||||||||||||||||||||||||||||||||||||||||||||||||||||||||||
Atommasse | 55,845(2)[3] u | ||||||||||||||||||||||||||||||||||||||||||||||||||||||||||||
Atomradius (berechnet) | 140 (156) pm | ||||||||||||||||||||||||||||||||||||||||||||||||||||||||||||
Kovalenter Radius | low-spin: 123 pm, high-spin: 152 pm | ||||||||||||||||||||||||||||||||||||||||||||||||||||||||||||
Elektronenkonfiguration | [Ar] 3d6 4s2 | ||||||||||||||||||||||||||||||||||||||||||||||||||||||||||||
1. Ionisierungsenergie | 7.9024681(12) eV[4] ≈ 762.47 kJ/mol[5] | ||||||||||||||||||||||||||||||||||||||||||||||||||||||||||||
2. Ionisierungsenergie | 16.19920(5) eV[4] ≈ 1562.98 kJ/mol[5] | ||||||||||||||||||||||||||||||||||||||||||||||||||||||||||||
3. Ionisierungsenergie | 30.651(12) eV[4] ≈ 2957.4 kJ/mol[5] | ||||||||||||||||||||||||||||||||||||||||||||||||||||||||||||
4. Ionisierungsenergie | 54.91(4) eV[4] ≈ 5298 kJ/mol[5] | ||||||||||||||||||||||||||||||||||||||||||||||||||||||||||||
5. Ionisierungsenergie | 75.00(15) eV[4] ≈ 7236 kJ/mol[5] | ||||||||||||||||||||||||||||||||||||||||||||||||||||||||||||
Physikalisch[2] | |||||||||||||||||||||||||||||||||||||||||||||||||||||||||||||
Aggregatzustand | fest | ||||||||||||||||||||||||||||||||||||||||||||||||||||||||||||
Modifikationen | vier[6] | ||||||||||||||||||||||||||||||||||||||||||||||||||||||||||||
Kristallstruktur | α-Eisen: kubisch raumzentriert γ-Eisen: kubisch flächenzentriert | ||||||||||||||||||||||||||||||||||||||||||||||||||||||||||||
Dichte | 7,874 g/cm3 = 7874 kg/m³ | ||||||||||||||||||||||||||||||||||||||||||||||||||||||||||||
Mohshärte | 4–5[7] | ||||||||||||||||||||||||||||||||||||||||||||||||||||||||||||
Magnetismus | ferromagnetisch | ||||||||||||||||||||||||||||||||||||||||||||||||||||||||||||
Schmelzpunkt | 1812 K (1539 ± 1[11][12] °C) | ||||||||||||||||||||||||||||||||||||||||||||||||||||||||||||
Siedepunkt | 3343 K (3070[13] °C) | ||||||||||||||||||||||||||||||||||||||||||||||||||||||||||||
Molares Volumen | 7,09·10−6 m3·mol−1 | ||||||||||||||||||||||||||||||||||||||||||||||||||||||||||||
Verdampfungsenthalpie | 354 kJ·mol−1[8] | ||||||||||||||||||||||||||||||||||||||||||||||||||||||||||||
Schmelzenthalpie | 13,8 kJ·mol−1 | ||||||||||||||||||||||||||||||||||||||||||||||||||||||||||||
Schallgeschwindigkeit | 4910 m·s−1 bei 293,15 K | ||||||||||||||||||||||||||||||||||||||||||||||||||||||||||||
Spezifische Wärmekapazität | 449[1] J·kg−1·K−1 | ||||||||||||||||||||||||||||||||||||||||||||||||||||||||||||
Austrittsarbeit | 4,5 eV[9] | ||||||||||||||||||||||||||||||||||||||||||||||||||||||||||||
Elektrische Leitfähigkeit | 10 · 106[10] S·m−1 | ||||||||||||||||||||||||||||||||||||||||||||||||||||||||||||
Wärmeleitfähigkeit | 80 W·m−1·K−1 | ||||||||||||||||||||||||||||||||||||||||||||||||||||||||||||
Chemisch[2] | |||||||||||||||||||||||||||||||||||||||||||||||||||||||||||||
Oxidationszustände | 2, 3, 4, 5, 6 | ||||||||||||||||||||||||||||||||||||||||||||||||||||||||||||
Normalpotential | −0,44 V (Fe2+ + 2 e− → Fe) | ||||||||||||||||||||||||||||||||||||||||||||||||||||||||||||
Elektronegativität | 1,83 (Pauling-Skala) | ||||||||||||||||||||||||||||||||||||||||||||||||||||||||||||
Isotope | |||||||||||||||||||||||||||||||||||||||||||||||||||||||||||||
| |||||||||||||||||||||||||||||||||||||||||||||||||||||||||||||
Weitere Isotope siehe Liste der Isotope | |||||||||||||||||||||||||||||||||||||||||||||||||||||||||||||
NMR-Eigenschaften | |||||||||||||||||||||||||||||||||||||||||||||||||||||||||||||
| |||||||||||||||||||||||||||||||||||||||||||||||||||||||||||||
Sicherheitshinweise | |||||||||||||||||||||||||||||||||||||||||||||||||||||||||||||
| |||||||||||||||||||||||||||||||||||||||||||||||||||||||||||||
Soweit möglich und gebräuchlich, werden SI-Einheiten verwendet. Wenn nicht anders vermerkt, gelten die angegebenen Daten bei Standardbedingungen. |
Eisen ist ein chemisches Element mit dem Symbol Fe (lateinisch ferrum ‚Eisen‘) und der Ordnungszahl 26. Es gehört zu den Übergangsmetallen, die im Periodensystem die 8. Nebengruppe (Eisen-Platin-Gruppe), nach der neuen Zählung die Gruppe 8 (Eisengruppe) bilden. Eisen ist, auf den Massenanteil (ppmw) bezogen, nach Sauerstoff, Silicium und Aluminium das vierthäufigste Element in der Erdkruste und nach Aluminium das häufigste Metall.
Auf der Erde kommt es, außer in verschiedenen Erzen und Eisenmineralien, in Form einer Legierung in Eisenmeteoriten vor. Aus diesen wurden schon vor der eigentlichen Eisenzeit, teilweise schon 3000 Jahre vor unserer Zeitrechnung, Kultgegenstände, Werkzeuge oder Waffen hergestellt. Es werden vor allem die Eisenerze Magnetit, Hämatit und Siderit abgebaut.
Chemisch reines Eisen ist ein silberweißes, verhältnismäßig weiches, dehnbares, recht reaktionsfreudiges Metall. Es wird als ferromagnetisches Material von Magneten angezogen und kann eigene Magnetfelder ausbilden. Reines Eisen wird in der Praxis relativ selten verwendet, aber es geht mit etwa 80 anderen Elementen Legierungen ein, deren wichtigste Stahl und Gusseisen sind. Diese besitzen für viele Industriezweige wie die Automobilindustrie, den Maschinenbau, das Bau- und Transportwesen und die Energieerzeugung eine unersetzliche wirtschaftliche und technische Bedeutung.
Eisen ist ein essentielles Spurenelement für fast alle Lebewesen. Bei Tieren ist es ein Bestandteil des Blutes in Form von Hämoglobin in den roten Blutkörperchen und auch für die Bildung von Proteinen und Enzymen von Bedeutung.
Begriffsverwendung und Wortherkunft
Neben dem chemischen Element als Reineisen wurden früher die praktisch viel bedeutsameren Eisenlegierungen meist als „Eisen“ bezeichnet (z. B. Schmiedeeisen). Im 20. Jahrhundert setzte sich für schmiedbare Eisenlegierungen mit einem Kohlenstoffanteil unter 2 Massenprozent die Bezeichnung „Stahl“ durch. Bei größerem Kohlenstoffanteil gilt weiterhin die Bezeichnung „Gusseisen“.
Bis in das 21. Jahrhundert wurde von Sprachwissenschaftlern (wie zum Beispiel Rudolf Thurneysen oder Stefan Schumacher[19]) angenommen, das keltische und germanische Wort für Eisen (keltisch *isarnon, germanisch *isarna) sei aus dem Illyrischen entlehnt worden. Auch wurde wegen des Gegensatzes zur weicheren Bronze eine Verwandtschaft von *isarnon zu lateinisch ira „Zorn, Heftigkeit“ vertreten.[20] Das neuhochdeutsche Wort Eisen (von mittelhochdeutsch īsen, und zu īsīn „eisern“) wird über althochdeutsch īsa(r)n, aus urgermanisch *īsarnan oder *eisarna-,[19] und dieses aus gallisch *īsarnon hergeleitet.[21] *isarnan und isarnon setzen sich außer im deutschen Eisen auch in den übrigen germanischen Sprachen (englisch iron, nordfriesisch joorn, westfriesisch izer, niederländisch IJzer) sowie in keltischen Sprachen fort (bretonisch houarn, kymr. haearn, irisches und schottisches Gälisch iarann, Manx yiarn). Deswegen werden seit Ende des 20. Jahrhunderts auch andere Entlehnungswege als möglich angenommen.[22][19]
Geschichte
Die ältere Kulturperiode der Bronzezeit ging nur sehr allmählich in die jüngere Eisenzeit über. Bei manchen Völkern, wie aus dem Gebiet des heutigen Indiens, denen leicht verhüttbare Eisenerze zur Verfügung standen, ist eine zeitliche Trennung kaum vorhanden.[23] Archäologen und Wissenschaftler für Technikgeschichte nehmen an, dass sich die Metallurgie von Eisen nur langsam gegen Bronze durchsetzte. So sind die als Nebenprodukt der Kupfer- und Bronzeherstellung in einfachen Rennöfen zufällig entstehenden Eisenschlacken durch den hohen Kohlenstoff- und Schwefelanteil spröde. Das direkt in solchen Öfen aus Eisenerzen ab etwa 2000 v. Chr. erzeugte Eisen ist recht weich, rostet leicht und ist damit Zinnbronze in den Eigenschaften unterlegen. Die Vorteile des Eisens gegenüber der Bronze lagen vor allem in der einfacheren Verarbeitung, weil nur ein Rohstoff benötigt wird. Erst mit der Verbreitung des Aufkohlens zum Stahl (zum Beispiel um 1000 v. Chr. auf Zypern) wurde es zum überlegenen Werkstoff.[24][25] Belege für die Nutzung von Eisen in den verschiedenen Kulturen durch archäologische Funde sind gegenüber den Funden von Bronze relativ selten. Zum einen wurde Eisen in den ältesten Perioden der Geschichte nur in geringem Umfang genutzt, zum anderen neigt Eisen an feuchter Luft, im Wasser und in der nassen Erde zur Korrosion, wodurch viele Gegenstände nicht erhalten blieben oder stark korrodierte Werkzeuge häufig wieder eingeschmolzen wurden. Nur besondere Umstände oder große Abmessungen des Gegenstandes verhinderten den Verlust solcher Stücke, so dass aus der Bronzezeit nur etwa 150 Eisenartefakte erhalten geblieben sind.[24][26]
Früheste Nutzung von Meteoriteneisen

Bevor Menschen in diversen Kulturkreisen lernten, Eisen aus Erz zu gewinnen, nutzten sie das bereits vor der eigentlichen „Eisenzeit“ bekannte und an seinem spezifischen Nickelgehalt von etwa 5 bis 18 % erkennbare Meteoreisen oder Meteoriteneisen. Wegen seiner Seltenheit war dieses „Himmelseisen“ (altägyptisch: bj-n-pt = „Eisen des Himmels“[27]) wertvoll und wurde vorwiegend zu Kultgegenständen und Schmuck verarbeitet. So wurden im Alten Ägypten in zwei Gräbern aus vordynastischer Zeit Schmuckperlen aus Meteoreisen mit einem Nickelgehalt von etwa 7,5 % gefunden,[28] die auf etwa 3200 v. Chr. datiert sind.[29] Ebenso konnte die schon früh geäußerte Vermutung bestätigt werden, dass ein als Grabbeigabe bei der Mumie des Pharao Tutanchamun gefundener Dolch von etwa 1350 v. Chr. aus Meteoreisen gefertigt worden war.[30] Die ältesten bekannten Funde aus Meteoreisen stammen aus Mesopotamien, das von den dort lebenden Sumerern als urudu-an-bar (= „Kupfer des Himmels“) bezeichnet wurde. Unter anderem wurde in der Stadt Ur ein Dolch mit einer Klinge aus Meteoreisen (10,8 % Nickel) und goldbelegtem Griff entdeckt, dessen Herstellung auf eine Zeit um 3100 v. Chr. datiert ist.[31] Ein weiterer Dolch mit einer Klinge aus Eisen wurde im Grab Tutanchamuns gefunden.
Eisenerzeugung aus Erz
Zu den Anfängen der Eisenverhüttung siehe
Mittelmeerraum und Kleinasien
Die Nutzung von nickelfreiem (also terrestrischem) Eisen muss in Mesopotamien ebenfalls schon früh erfolgt sein. Als Beleg dafür dient ein nickelfreier Eisendolch mit Bronzegriff aus der Zeit zwischen 3000 und 2700 v. Chr., der in den Ruinen von Ešnunna bei Tell Asmar im heutigen Irak gefunden wurde.[31] Aus den Aufzeichnungen der Hethiter im Archiv von Boğazkale (ehemals Boğazköy) in Zentralanatolien geht hervor, dass Eisen bereits zur Zeit von König Anitta (etwa 1800 v. Chr.) bekannt war und die Verhüttung von Eisen mindestens seit etwa 1300 v. Chr. erfolgte.[32][33] Zwischen 1600 und 1200 v. Chr. spielte die Eisentechnologie des Hethitischen Reiches eine Pionierrolle und gilt als ein wichtiger Faktor für dessen Aufstieg.[34][35][24] Die Hethiter stellten aus dem Eisen, das anfänglich mit bis zum achtfachen Gewicht in Gold aufgewogen wurde,[36] zunächst vorwiegend Schmuck her.[37] In der späten Hethiterzeit war Eisen schon so weit verbreitet, dass es in Inventarlisten nicht mehr mit den Edelmetallen, sondern zusammen mit Kupfer geführt wurde. Einzelstücke aus terrestrischem Eisen aus der Mittleren und Späten Bronzezeit fanden sich aber nicht nur bei den Hethitern, sondern auch in Griechenland und Zypern, in Jordanien, Libanon, Israel und Ägypten.[24] Ab 1200 v. Chr. wurde in der Levante Stahl produziert, das heißt Eisen mit erhöhtem Kohlenstoffanteil.[36]
Der Beginn der Eisenzeit wird für den Nahen Osten im Allgemeinen auf das Jahr 1200 v. Chr. festgesetzt – nicht weil Eisen ab diesem Zeitpunkt eine nennenswerte Rolle spielte, sondern weil innerhalb kürzester Zeit die Kulturen der Bronzezeit kollabierten. Die ersten Jahrhunderte der Eisenzeit sind in dieser Region ein „dunkles Zeitalter“, in dem viele Städte zerstört wurden, der Fernhandel zusammenbrach und die Metallproduktion nahezu zum Erliegen kam. Erst ab etwa 700 v. Chr., als sich die Kulturen wieder vom Zusammenbruch zu erholen begannen, kam Eisen wieder häufiger zum Einsatz. Seit 1200 v. Chr. ist in dieser Region der nach der Stadt Damaskus genannte Damaszener Stahl oder Schmelzdamast bekannt, der einen sehr hohen Kohlenstoffgehalt von etwa 1,5 % und beim Polieren ein charakteristisches Muster aufweist. Dieser Werkstoff ist jedoch nicht nur im Nahen Osten, sondern bereits früher in anderen Regionen bekannt, so zum Beispiel in Südindien, wo er spätestens seit 300 v. Chr. hergestellt wird.[24]
Im alten Ägypten ist die Verhüttung von Eisen erst seit dem 6. Jahrhundert v. Chr. nachgewiesen. Gleichwohl wurde bereits im Alten Reich Meteoriteneisen vor allem zur Herstellung von Amuletten und Modellwerkzeugen für das Mundöffnungsritual verwendet.[38] Ein Eisenfund in einem Grab bei Abydos aus der 6. Dynastie (2347–2216 v. Chr.) ließ sich zwar als nickelfrei und damit terrestrischen Ursprungs bestimmen; sein früherer Verwendungszweck konnte jedoch nicht ermittelt werden, da das Stück völlig verrostet war.[28] Ein 1837 in den Fugen der Cheops-Pyramide gefundenes Eisenmesser, das zunächst in die 4. Dynastie datiert wurde,[39] erwies sich hingegen als modernes Stück.[40]
Die Chalyber zählten zu den Völkern des Mittelmeerraums und Kleinasiens, die gute Kenntnisse über die Nutzung des Eisens als Hüttenwerkstoff gewonnen hatten. Ihr Name lebte in dem griechischen Wort für Stahl (chalybs) weiter, im Gegensatz zum gewöhnlichen Eisen (sideros).[41] Früheste Spuren von Eisenverhüttung auf griechischem Gebiet fanden sich in Form von Eisenschlacke aus der Zeit um 2000 v. Chr. in Agia Triada auf Kreta.[42]
In Gerar (Palästina) war die Eisenverhüttung etwa ab 1000 v. Chr. bekannt (belegt durch Eisenschmelzöfen und örtlich hergestellte Ackerbaugeräte[41]).
Europa

Zu den ältesten europäischen Stücken gehören die eisernen Zelte und Speere, die Graf Gozzadini 1853 in etruskischen Gräbern bei Bologna entdeckt hat. Sie stammen aus dem 9. bis 10. Jahrhundert vor Christus.[43] In Mitteleuropa allgemein wird die vorrömische Eisenzeit üblicherweise in Hallstattzeit (800–450 v. Chr.) und Latènezeit (ab 450 v. Chr.) unterteilt, wobei erste Eisenobjekte in der späten Bronzezeit aufgetaucht waren.[24]
Einer der ältesten bekannten Eisenfunde in Deutschland ist ein eiserner Niet als Verbindung zwischen bronzener Lanzenspitze und hölzernem Schaft, der in Helle (Ostprignitz) gefunden wurde und etwa aus der Zeit um 800 v. Chr. stammt.[41] Im deutschsprachigen Raum markiert die erst etwa 300 Jahre später im gesamten keltischen Kulturkreis beginnende La-Tène-Zeit eine erste Hochkultur mit zahlreichen Eisenverhüttungsplätzen und Eisenfunden (zum Beispiel im Siegerland und in Teltow).[24][44] In Norddeutschland blieben in der Hallstattzeit die bronzezeitlichen Kulturen bestehen. Südlich der Alpen gab es hingegen mit den Etruskern eine Hochkultur, die große Mengen an Bronze und Eisen herstellte und deren Produkte bis nach Mitteleuropa kamen. Sie bauten unter anderem einen Eisenskarn auf Elba ab.[24]
Vom frühen zweiten Jahrtausend vor Christus bis ins 18. Jahrhundert waren Rennöfen beziehungsweise Rennwerke mit angeschlossenen Schmieden in Europa weit verbreitet. Dies waren einfache, häufig in den Boden eingelassene mit Holzkohle betriebene Herde von einigen Dezimetern Durchmesser und ebensolcher Höhe. Flüssiges Roheisen entstand mit diesem Verfahren nicht, da ein Rennofen nur Temperaturen zwischen 1000 und 1200 °C erreichen konnte, der Schmelzpunkt von reinem Eisen jedoch bei 1538 °C liegt (Schmelzpunkt von reinem Zementit, Fe3C: 1250 °C). Die Rennöfen waren bis ins späte Mittelalter die einzige Methode, um schmiedbares Eisen herzustellen. Bereits in der Zeit um die Geburt Christi erreichte die Eisenproduktion teilweise industrielle Ausmaße. So wird zum Beispiel die Gesamtzahl von vorhandenen Öfen, der in mehreren Zentren im Weichselbogen errichteten Eisenhütten, auf eine Größenordnung von 100.000 bis 200.000 geschätzt. Das Gebiet erstreckt sich von wenigen Kilometern westlich von Warschau bis in das Bergland östlich Kielce. Eine systematische Erforschung des Gebietes ergab, dass die Eisenherstellung zwischen 150 vor und 150 nach Christus ihre höchste Betriebsintensität gehabt haben muss. In Katalonien wurden ab dem 8. Jahrhundert und im Hochmittelalter in vielen Gegenden von Mitteleuropa zunehmend Rennöfen mit von Wasserrädern betriebenen Blasebälgen gebaut, die die Glut mit Sauerstoff versorgten. Diese weiterentwickelten und größeren Öfen wurden „Stücköfen“ oder „Wolfsöfen“ genannt und mussten daher an Wasserläufen gebaut werden. Sie erreichten deutlich höhere Temperaturen, die in einem Teil des Ofens den Schmelzpunkt von Eisen überschreiten konnten. Ab diesem Zeitpunkt erlaubte das „Frischen“ eine Verringerung des Kohlenstoffgehalts im Roh- oder Gusseisen.[25][24] Die frühesten Gusseisenstücke aus ersten einfachen Hochöfen wurden in Schweden (Lapphyttan und Vinarhyttan) entdeckt und auf 1150 bis 1300 datiert.[45] Die ab dem 13. Jahrhundert eingesetzten Floßöfen erlaubten ein kontinuierliches Schmelzen.[46] Mit der gegossenen Kanonenkugel (ab 1400[47]) verbreitete sich die Gusseisenverarbeitung schnell wie die Feldzüge über ganz Europa.
Da die schwindenden Wälder in Europa den wachsenden Bedarf an Holzkohle für die Eisenerzeugung nicht mehr decken konnten, wurde nach Alternativen gesucht. Als Erstem gelang 1709 Abraham Darby in Großbritannien der Einsatz von Kohle (genauer dem Kohleprodukt Koks) als Alternative. In Deutschland wurde erst 1796 ein rein auf Koks ausgelegter Hochofen in Betrieb genommen.[48][49] Diese Umstellung, zusammen mit der Erfindung der Dampfmaschine, gilt als Beginn der industriellen Revolution. Die Hüttenwerke produzierten Gusseisen und Schmiedeeisen. Mit der Einführung des Puddelverfahrens um 1784 konnte die bisher übliche Holzkohle durch die günstigere Steinkohle ersetzt werden.[24]
Eisennutzung und Funde außerhalb Europas und Kleinasiens
In Afrika gab es eine sehr alte Tradition der Eisenproduktion, die vor etwa 3000 Jahren begann. Die afrikanischen Metallurgen waren sehr experimentierfreudig und innovativ, die Konstruktionsweisen und Formen der Öfen weisen eine Vielfalt auf, die auf anderen Kontinenten nicht zu finden ist. Bis auf wenige Ausnahmen – nämlich Mauretanien und Niger – gab es an den meisten Fundorten südlich der Sahara keine Kupfer- oder Bronzezeit, die der Eisenverhüttung vorausging: Auf das Neolithikum folgte direkt die Eisenzeit. Den ältesten bekannten Schmelzofen in Afrika, der im Termit-Massiv im Niger entdeckt wurde, datierten Archäologen auf 800 v. Chr. Weitere Fundstätten für die Eisenverarbeitung wurden zum Beispiel in Walalde im Senegal, in der Zentralafrikanischen Republik, in Ruanda, in Taruga, der Region um Nsukka und am Nordrand des Mandaragebirges im Grenzgebiet zwischen Nigeria und Kamerun entdeckt.[24]
Ab dem 7. Jahrhundert v. Chr. war Eisen außer bei den Kulturen im Nahen Osten und Teilen Europas auch in vielen weiteren Regionen bekannt: so in Indien und Sri Lanka, in China, in Osteuropa bei den Skythen und südlich der Sahara in Afrika. In Kolchis, das heutige westliche Georgien, war im 7. Jahrhundert ein wichtiger Eisenproduzent. Dort wurden etwa 400 Öfen gefunden, in denen Hämatit und Magnetit verhüttet wurden.[24]
In China wurden die ersten Erfahrungen mit Eisen an Meteoriteneisen gewonnen. Erste archäologische Spuren von Schmiedeeisen finden sich im Nordwesten, nahe Xinjiang, aus dem 8. vorchristlichen Jahrhundert. Es wird vermutet, dass diese Produkte, die mit den Methoden des Nahen Ostens erstellt wurden, durch Handel nach China gelangt sind. Das änderte sich in der späten Zhou-Zeit im 5. Jahrhundert v. Chr. mit einer massenhaften Produktion von Gusseisen in Hochöfen im Staat Wu, der im Südosten Chinas lag.[24][50] Die Verhüttung von Eisen in Zentralchina ist mindestens seit der Han-Dynastie (206 v. Chr. bis 222 n. Chr.) belegt.[50] China entwickelte die Technologie kontinuierlich weiter und blieb ein sehr innovatives Zentrum der Metallurgie.[24]
In den Gräbern von Turan, einer Region, die sich über den Osten Irans, den Süden Afghanistans und den Südwesten Pakistans zog, fanden sich eiserne Gegenstände und größere Eisenlager in den Ruinen von Khorsabad, welches 612 v. Chr.[51] zerstört wurde. Entdeckt wurden von Victor Place Ringe und Kettenteile zusammen mit etwa 160.000 kg Eisenbarren.[52] Layard stieß bei seinen Ausgrabungen in Nimrud auf eiserne Waffen wie Helme, Speere und Dolche.[53] Berühmt ist die Eiserne Säule in Delhi, ein sieben Meter hoher schmiedeeiserner Pfeiler aus dem 4./5. Jahrhundert.[54]
In Australien und den umliegenden besiedelten Inseln Polynesiens war dagegen die Nutzung von Eisen bis zur Entdeckung durch europäische Forscher unbekannt. Die ansonsten hohe Kultur der Inkas und Azteken in Mittel- und Südamerika verarbeitete ebenfalls Gold, Silber, Kupfer und Bronze in guter Qualität und mit großem Geschick, Eisen jedoch nur in geringen Mengen und nur Meteoreisen.[55] In Nordamerika wurde 1621 in North Carolina mit dem Bau der ersten Eisenhütte begonnen.[47]
Spätere Entwicklung
Die Mitte des 18. Jahrhunderts beginnende industrielle Revolution zog eine rasche Erfindung von Maschinen und deren Einsatz nach sich. Dadurch stieg nicht nur die Nachfrage nach Rohstoffen wie Eisen rapide, auch der Einsatz von Maschinen im Bergbau, in der Verhüttung und weiteren Bereichen nahm zu. Wenige Jahrzehnte später gab es die ersten Spinnmaschinen, Eisenbahnen und Schiffe aus Eisen. Noch Ende des 18. Jahrhunderts entstanden die ersten Brücken aus Gusseisen. Im 19. Jahrhundert wurde eine Reihe neuer Stahlherstellungs- und Verarbeitungsverfahren entwickelt und eingesetzt. 1810 wurde die Konservendose aus Blech patentiert. 1814 nahm Berzelius das Eisen als Ferrum in seine Atomgewichtstabelle mit auf. 1834 erfand in Clausthal Julius Albert das Drahtseil, das Hanfseile und Eisenketten ersetzte. 1845 wurde im Saarland das erste Walzwerk zur Herstellung von Eisenbahnschienen in Betrieb genommen. Im Jahr 1855 wurden zur Stahlherstellung das Bessemer-, 1864 das Siemens-Martin- und 1879 das Thomas-Verfahren entwickelt. In London wurde für die erste Weltausstellung im Jahr 1851 der Kristallpalast gebaut, ein riesiges Ausstellungsgebäude aus Gusseisen und Glas. 1859 produzierte Alfred Krupp erstmals Geschütze aus Stahl. Generell besitzen Firmen der Stahlindustrie, wie in Deutschland Krupp, Thyssen und Gutehoffnungshütte (heute MAN), seit dieser Zeit eine große wirtschaftliche Bedeutung. Für die Weltausstellung 1889 in Paris wurde der Eiffelturm und für die Weltausstellung 1958 wurde mit dem Atomium die milliardenfache Vergrößerung der kristallinen Elementarzelle des Eisens errichtet.[56][24][57] Bereits 1912 erlangte Eisen im Gemisch mit anderen Metallen als Katalysator bei der Synthese von Ammoniak im Haber-Bosch-Verfahren eine große industrielle Bedeutung.[58] Bei der 1921 entwickelten Fischer-Tropsch-Synthese von Kohlenwasserstoffen aus Synthesegas spielen Eisenkatalysatoren eine wichtige Rolle.[59][60] Bis 1925 stieg die jährliche Welterzeugung von Stahl auf rund 100 Millionen Tonnen und in den folgenden 50 Jahren auf rund 700 Millionen Tonnen.[47] Nach 2010 überschritt sie den Wert von 1,5 Milliarden Tonnen.[61] In Deutschland betrug die Produktion von Rohstahl im Jahr 2020 etwa 35 Millionen Tonnen.[62]
Der Preis für Stahl variiert je nach Art des Stahls und den Marktbedingungen, Angebot und Nachfrage stark. So stieg der reale Preis im Ersten Weltkrieg von rund 300 US$/t auf 941 US$/t im Juli 1917 und fiel gegen Ende des Krieges auf etwa 450 US$/t. Nach einem Anstieg durch die beiden Ölpreiskrisen in den 1970er Jahren sank der Preis um 1982 wieder auf dieses Niveau. Infolge einer steigenden Stahlnachfrage stieg der Preis in der Folgezeit wieder, erreichte 1990 etwa 600 US$/t und im Juli 2008 einen Rekordwert von fast 1.280 US$/t. Als Folge der Weltfinanzkrise und deren Auswirkung in Europa sank der Preis im März 2009 erneut auf einen Wert unter 450 US$/t, stieg jedoch schnell wieder auf über 720 US$/t im Juli 2011.[63] Nach einem Rückgang der Preise infolge der COVID-19-Pandemie stieg der Preis 2022 teilweise auf 1500 US$/t.[64]
Eisenverbindungen
Neben Eisen selbst sind auch seine Verbindungen von historischer Bedeutung. Schwefelkies (Pyrit und Markasit, Eisen(II)-disulfid) wurde zum Funkenschlagen in steinzeitlichen Schlagfeuerzeugen verwendet, die in Europa vor etwa 40.000 Jahren aufkamen.[65] Natürliche Eisenoxidpigmente sind aufgrund ihrer Farbechtheit in Höhlenmalereien von 35.000 v. Chr. nachweisbar. Mit einer Weltjahresproduktion von über 500.000 t an synthetischen und 100.000 t an natürlichen Produkten in den 2010er Jahren stellen sie die mit Abstand wichtigste Gruppe der Buntpigmente dar. Sie sind preisgünstige anorganische Farbstoffe und finden breite Anwendung vor allem in Baustoffen und Beschichtungsmitteln.[66] Der Einsatz von Eisenpräparaten als Arzneistoff ist schon seit der Antike (zum Beispiel zur Heilung von Iphiklos) beschrieben.[67][68] Neben Eisenoxidpigmenten hatten Eisenblaupigmente als Metallkomplexe eine wirtschaftliche Bedeutung. Diese weisen hohe Färbekraft und hohe Licht- und Wetterbeständigkeit auf und waren Bestandteil blauer Lacke und Anstrichfarben. Eisenblau wurde um 1700 in Berlin von Johann Jacob Diesbach als Niederschlag bei einer Fällungsreaktion beobachtet und von A. Milori im frühen 19. Jahrhundert industriell hergestellt. Pigmente dieser Gruppe gewannen rasch an Bedeutung, bevor sie diese ab etwa 1970 an Phthalocyanin-Blau verloren haben.[69] Das erstmals 1752[70] von Pierre-Joseph Macquer aus Berliner Blau und Kalilauge hergestellte gelbe Blutlaugensalz hatte bis zum Ende des 19. Jahrhunderts eine große wirtschaftliche Bedeutung.[71] Das 1851 entdeckte Eisenpentacarbonyl erlangte kurzfristig eine wichtige Rolle. Nachdem es sich als sehr wirksames Antiklopfmittel für Ottomotoren erwiesen hatte, baute BASF 1925 eine große Produktionsanlage. Als die Verbindung kurz darauf durch Bleialkyle als Antiklopfmittel ersetzt wurde, verlor sie an Bedeutung und wurde nur noch zur Herstellung von Eisenpulver zum Beispiel für die Pulvermetallurgie eingesetzt.[72] Das Mitte des 20. Jahrhunderts entdeckte Ferrocen und seine Derivate wurden aufgrund ihrer Eigenschaften in der Grundlagenforschung untersucht und in der Katalyse, der Sensorik und der Medizin eingesetzt.[73]
Vorkommen



Eisen steht in der Reihe der relativen Elementhäufigkeit bezogen auf Silicium im Universum mit 8,7 · 105 Atomen je 1 · 106 Siliciumatomen an 9. Stelle.[74] Die Fusion von Elementen in Sternen endet beim Eisen (genauer bei 56Fe), da bei der Fusion höherer Elemente keine Energie mehr frei wird (siehe Nukleosynthese), die Elementisotope instabil sind oder kein einfacher Syntheseprozess existiert.[75] Eisen selbst entsteht vor allem beim Siliciumbrennen in schweren Sternen.[76] Massereiche Sterne mit einer Masse größer als dem Achtfachen der Sonnenmasse fusionieren in ihrem Kern fast alle leichteren Elemente zu Eisen. Schwerere Elemente entstehen endotherm bei Supernovaexplosionen, die auch für das Verstreuen der im Stern entstandenen Materie verantwortlich sind.[77] Die Kruste von Neutronensternen besteht hauptsächlich aus Eisenkernen.[78] In der Photosphäre unserer Sonne sind 0,16 % Eisen enthalten.[79]
Viele Planeten, darunter die Gesteinsplaneten und die Metallosilikatplaneten (wie zum Beispiel Merkur, Venus und die Erde) besitzen einen Eisenkern. Bei den hypothetischen Eisenplaneten fehlt der darüber liegende Erdmantel zum großen Teil oder vollständig, wodurch Eisen einen hohen Anteil an der Gesamtmasse des Planeten hat.[80] Auch bei anderen astronomischen Objekten, wie Monden, einigen Asteroiden und Eisenmeteoriten, ist ein hoher Eisenanteil normal. So wird beim Erdmond davon ausgegangen, dass dessen Kern vorwiegend aus Eisen besteht.[81] Das weite Areale der Mondoberfläche bedeckende Regolith enthält im geringen Prozentbereich Eisen in Form von Eisen(II)-oxid.[82]
Auf der Erde steht Eisen in der Reihe der Elementhäufigkeit nach dem Massenanteil an 2. Stelle in der gesamten Erde (28,8 %[83]), an 4. Stelle in der Erdhülle (4,70 %[1]) und an 4. Stelle in der kontinentalen Erdkruste (5,63 %[84]); im Meerwasser ist es nur zu 0,002 mg/L[85] enthalten. Eisen ist zusammen mit Nickel wahrscheinlich der Hauptbestandteil des Erdkerns. Vermutlich angetrieben von thermischen Kräften erzeugen Konvektionsströmungen von flüssigem Eisen im äußeren Kern das Erdmagnetfeld.[86]
Das meiste Eisen in der Erdkruste ist mit verschiedenen anderen Elementen verbunden und bildet mehrere hundert verschiedene Eisenmineralien.[87] Eine wichtige und wirtschaftlich bedeutsame Klasse sind die Eisenoxidmineralien wie Hämatit (Fe2O3), Magnetit (Fe3O4) und Siderit (FeCO3), Limonit (Fe2O3·n H2O) und Goethit (FeO·OH), die die Haupterze des Eisens sind.[88] Viele magmatische Gesteine enthalten das Sulfidmineral Pyrrhotin und das mit ihm verwachsene Nickel-Eisen-Mineral Pentlandit.[89] Während der Verwitterung neigt Eisen dazu, aus Sulfidablagerungen als Sulfat und aus Silicatablagerungen als Hydrogencarbonat herauszulösen. Beide werden in wässriger Lösung oxidiert und fallen in Form von Eisen(III)-oxid bei leicht erhöhtem pH-Wert aus.[90]
Große Eisenvorkommen sind Bändererze, eine Art Gestein, das aus wiederholten dünnen Schichten von Eisenoxiden besteht, die sich mit Bändern aus eisenarmem Schiefer und Kieselgestein (Chert) abwechseln. Die Bändererze wurden hauptsächlich in der Zeit zwischen vor 3700 Millionen Jahren und vor 1800 Millionen Jahren abgelagert (die jüngsten entstanden vor 350 Millionen Jahren), durch Reaktion von Eisen mit dem durch cyanobakterielle Photosynthese entstehenden Sauerstoff.[91]
Materialien, die fein gemahlene Eisen(III)-oxide oder -oxidhydroxide wie Ocker enthalten, werden seit vorgeschichtlicher Zeit als gelbe (Ocker), rote (Hämatit), braune (Umbra) und schwarze (Magnetit) Pigmente verwendet.[92] Sie tragen zur Farbe verschiedener Gesteine und Tone bei, einschließlich ganzer geologischer Formationen wie der Painted Hills in Oregon[93] und des Buntsandsteins.[94] Durch Eisensandstein in Deutschland und Bath Stone in Großbritannien sind Eisenverbindungen für die gelbliche Farbe vieler historischer Gebäude und Skulpturen verantwortlich. Die sprichwörtliche rote Farbe der Marsoberfläche stammt von einem eisenoxidreichen Regolith.[95]
Im Eisensulfidmineral Pyrit (FeS2) sind erhebliche Eisenmengen enthalten. Es dient jedoch hauptsächlich zur Produktion von Schwefelsäure, wobei die bei der Produktion entstehenden Kiesabbrände einen hohen Eisengehalt besitzen.[96] Es ist nur mit modernen Verfahren, möglich diese zur Eisengewinnung zu nutzen, da hierzu Reste des Schwefels entfernt werden müssen, die das Eisen brüchig werden lassen.[97] Aus diesem Grund und weil Eisenerze so verbreitet sind, konzentriert sich die Eisenproduktion anstelle von Pyrit auf Erze mit sehr hohem Eisengehalt.[92]
Das langlebige Eisenisotop Fe60 kann unter anderem in Tiefseesedimenten nachgewiesen werden. Wissenschaftler erklären dies mit dem Eintrag des durch Supernovas entstandenen Isotops durch Mikrometeorite auf die Erde. Die Verteilung und Häufigkeit der Isotope kann zur Datierung der Sedimente und indirekt der kosmischen Ereignisse verwendet werden.[98][99]
Eisen in Erzen
Die ersten Vorkommen, die abgebaut wurden, waren Raseneisenstein und offenliegende Erze. Heute werden vor allem Magnetit (Fe3O4), Hämatit und Siderit abgebaut.[92] Die größten Eisenerzvorkommen finden sich in den sogenannten Banded Iron Formations (BIF, gebändertes Eisenerz oder Bändererz), die auch als Takonit oder Itabirit bezeichnet werden und Eisen hauptsächlich in den Mineralen Hämatit und Magnetit (durch sekundäre Prozesse entstanden) enthalten.[100]
Eisen als Mineral

Selten kommt Eisen in der Natur gediegen vor, meist in Form kleiner Bläschen oder Verdickungen im umgebenden Gestein, aber auch als massige Mineral-Aggregate mit bis zu 25 t Gewicht,[101] und ist deshalb als Mineral anerkannt.
Weltweit sind bisher rund 2000 Vorkommen für gediegen Eisen dokumentiert (Stand: 2024), wobei die überwiegende Mehrheit aus meteoritischen Eisenfunden der Varietät Kamacit besteht.[102]
Da gediegen Eisen bereits lange vor der Gründung der International Mineralogical Association (IMA) bekannt und als eigenständige Mineralart anerkannt war, wurde dies von ihrer Commission on New Minerals, Nomenclature and Classification (CNMNC) übernommen und bezeichnet es als sogenanntes „grandfathered“ (G) Mineral.[103] Die ebenfalls von der IMA/CNMNC anerkannte Kurzbezeichnung (auch Mineral-Symbol) für Eisen entspricht dem Elementsymbol „Fe“.[104]
Die IMA führt Eisen zusammen mit Chrom, Vanadium und Wolfram gemäß der Systematik der Minerale nach Strunz (9. Auflage) unter der System-Nr. „1.AE.05“ (Elemente – Metalle und intermetallische Verbindungen – Eisen-Chrom-Familie – Eisengruppe)[105] (8. Auflage: I/A.04a bzw. nachfolgende Lapis-Systematik nach Weiß: I/A.07). Die im englischsprachigen Raum ebenfalls geläufige Systematik der Minerale nach Dana führt das Element-Mineral unter der System-Nr. „01.01.11.00“.
Eisen kristallisiert im kubischen Kristallsystem, hat je nach Bildungsbedingungen und Reinheitsgrad eine Mohshärte zwischen 4 und 5[7] und eine stahlgraue bis schwarze Farbe (Eisenschwarz[106]). Die Strichfarbe ist grau.
Wegen der Reaktion mit Wasser und Sauerstoff (Rosten) ist gediegen Eisen nicht stabil. Es tritt daher in Legierung mit Nickel entweder als Kamacit (4 bis 7,5 % Ni) oder Taenit (20 bis 50 % Ni) nur in Eisenmeteoriten auf sowie in Basalten, in denen es manchmal zu einer Reduktion von eisenhaltigen Mineralen kommt. Eisen mit geringeren Nickelanteilen gilt als Varietät desselben und ist unter der Bezeichnung Josephinit bekannt;[107] diese Bezeichnung ist auch ein Synonym des Minerals Awaruit (Ni3Fe).[108]
Eisenerze hingegen sind vergleichsweise häufig zu finden; wichtige Beispiele sind die Minerale Magnetit (Magneteisenstein, Fe3O4), Hämatit (Roteisenstein, Fe2O3), Pyrrhotin (Magnetkies, FeS), Pyrit (Eisenkies, FeS2), Siderit (Eisenspat, FeCO3) und das als Gestein geltende Limonit (Brauneisenstein, Fe2O3·n H2O). Das Sedimentgestein Eisen-Oolith, manchmal als Eisenstein bezeichnet, besteht aus Eisenhydroxidmineralien, verkittet mit tonigen oder kalkigen Bindemitteln. Industriell weniger von Interesse, doch in der Natur ziemlich häufig anzutreffen sind die Minerale Chlorit, Glaukonit und Pyrit. Im Jahr 2024 waren insgesamt 1424 Eisenminerale bekannt.[109]
Eisen in Lebensmitteln
Viele Lebensmittel enthalten Eisen in Spuren. So enthält Hafer (entspelzt) 58 mg/kg, Gerste (entspelzt) und Roggen 28 mg/kg, Weizen 33 mg/kg, Kakao (schwach entölt) 125 mg/kg, Spinat 38 mg/kg, Kartoffel 5 mg/kg, Petersilie 55 mg/kg, Rote Bete 9 mg/kg, Apfel 2 bis 9 mg/kg, Rindfleisch 21 mg/kg, Rinderleber 70 mg/kg, Rinderniere 11 mg/kg, Schweineleber 154 mg/kg, Schweinefleisch 18 mg/kg, Schweinenieren 100 mg/kg, Schweineblut 550 mg/l, Rinderblut 500 mg/l, Kuhmilch 0,5 mg/l und Eigelb 60 bis 120 mg/l.[110]
Förderung

Die Volksrepublik China ist mit 888 Millionen Tonnen (67,8 %) das im Jahr 2020 bei weitem bedeutendste Herstellerland für Roheisen, gefolgt von Indien mit 68 Millionen Tonnen (5,2 %), Japan mit 62 Millionen Tonnen (4,7 %) und Russland mit 52 Millionen Tonnen (4,0 %). Die vier Staaten hatten zusammen einen Anteil von 81,7 % an der Weltproduktion von 1310 Millionen Tonnen. In Europa waren weitere wichtige Produzenten die Ukraine, Deutschland und Frankreich.[61]
Weltweit wurden 2020 etwa 2,5 Milliarden Tonnen Eisenerz abgebaut. Bedeutende Eisenerzlieferanten waren Australien, gefolgt von Brasilien, der Volksrepublik China, Indien und Russland. Zusammen hatten sie einen Anteil von 79,5 % an der Weltförderung. Zusätzlich wird aus Schrott noch neues Eisen hergestellt.[111]
Rang | Land | Produktion (in Mio. t) |
Rang | Land | Produktion (in Mio. t) | |
---|---|---|---|---|---|---|
1 | ![]() |
700,7 | 11 | ![]() |
14,9 | |
2 | ![]() |
80,2 | 12 | ![]() |
12,5 | |
3 | ![]() |
77,3 | 13 | ![]() |
9,7 | |
4 | ![]() |
51,9 | 14 | ![]() |
7,6 | |
5 | ![]() |
46,3 | 15 | ![]() |
6,1 | |
6 | ![]() |
35,0 | 16 | ![]() |
6,1 | |
7 | ![]() |
27,3 | 17 | ![]() |
6,0 | |
8 | ![]() |
22,3 | 18 | ![]() |
5,6 | |
9 | ![]() |
21,9 | 19 | ![]() |
5,2 | |
10 | ![]() |
18,3 | 20 | ![]() |
5,0 |
Entwicklung der weltweiten Eisenerzförderung (in Millionen Tonnen)[112][111] ![]() |
Entwicklung der weltweiten Rohstahlerzeugung (in Millionen Tonnen)[113][61] ![]() |
Gewinnung und Darstellung


Erzgewinnung und -verarbeitung
Eisenerz wird hauptsächlich im Tagebau und seltener im Tiefbau (Untertagebau, wie im Eisenerzbergwerk Kiruna) gewonnen. Wo die als abbauwürdig erkannten Eisenerzlagerstätten offen zutage treten, kann das Erz im weniger aufwändigen Tagebau gewonnen werden. Der Großteil des Eisenerzes wird in Brasilien, Australien, China, Indien, den USA und Russland abgebaut.[114][115]
Diese Länder verdrängten die ursprünglich bedeutendsten Eisenerz-Förderländer wie Frankreich, Schweden und Deutschland, dessen letzte Eisenerzgrube in der Oberpfalz 1987 geschlossen wurde.[116][117]
Aus technologisch-wirtschaftlichen Gründen sollten die zur Verarbeitung in Hochöfen eingesetzten Erze in chemischer und physikalischer Sicht gleichmäßige Eigenschaften besitzen. Demnach müssen die beim Abbau gewonnenen groben Erze gebrochen, gemahlen und gesiebt und die zu feinen Erze stückig gemacht werden. Das wird als Erzvorbereitung bezeichnet. Ungleichmäßigkeiten der Erze eines Abbauortes oder verschiedener Abbauorte werden durch Mischen der Erze auf sogenannten Mischbetten ausgeglichen. Nur ein kleiner Teil der Erze kann als Stückerz direkt im Hochofen eingesetzt werden.[118] Der Hauptanteil der Eisenerze liegt als Feinerz vor und muss für den Einsatz im Hochofen stückig gemacht werden, da das feine Erz die Luftzufuhr (Wind) im Hochofen sehr beeinträchtigen oder verhindern würde.[119] Die wichtigsten Verfahren dafür sind Sinterung und Pelletierung. In Deutschland werden die Erze vorwiegend durch Sintern stückig gemacht. In anderen Ländern, beispielsweise in den USA, wird mehr pelletiert, wobei die bei der Aufbereitung anfallende Korngröße entscheidend für die Auswahl des Verfahrens ist. Das Sintern erfordert eine Korngröße von mehr als 2 mm, während noch feiner aufgemahlene Erze pelletiert werden.[118]
In den Sinteranlagen werden gröbere Erzkörner nach ihrer Größe sortiert und gesintert. Kleine Erzkörner müssen dazu gemeinsam mit Kalkzuschlagsstoffen auf mit Gas unterfeuerte, motorisch angetriebene Wanderroste (Rost-Förderbänder) aufgebracht und durch starke Erhitzung angeschmolzen und dadurch „zusammengebacken“ (gesintert) werden. Sehr feines Erz wird pulverfein aufgemahlen, was oft bereits zur Abtrennung von Gangart nötig ist. Dann wird es mit Kalkstein, feinkörnigem Koks (Koksgrus) und Wasser intensiv vermischt und auf einen motorisch angetriebenen Wanderrost aufgegeben. Durch den Wanderrost werden von unten Gase abgesaugt. Von oben wird angezündet und eine Brennfront wandert von oben nach unten durch die Mischung, die dabei kurz angeschmolzen (gesintert) wird. Beim Pelletieren wird mit Bindemitteln, Zuschlägen und Wasser eine Mischung erzeugt, die auf Pelletiertellern zu Kügelchen (Grünpellets) von 8 bis 18 mm Durchmesser[120] gerollt wird. Diese werden mit Gasbefeuerung bei 1000 °C auf einem Wanderrost, in Schachtöfen oder Drehrohröfen zu Pellets gebrannt. Sinter ist nicht gut transportierbar und wird deshalb im Hüttenwerk erzeugt, Pelletanlagen werden meist in der Nähe der Erzgruben betrieben.[119][118]
Eisenherstellung
Zur Herstellung von Eisen müssen die in Form von Eisenoxide oder -Sulfide vorliegenden Erze chemisch reduziert werden. Zur Herstellung von Roheisen in Hochöfen werden diesen aufbereiteten Erze (Sinter oder Pellets) mit einer Beimischung von Zuschlägen zugeführt. Daneben wird eine hohe Menge Energie benötigt, die meist durch Koks oder alternativ auch Erdgas oder Wasserstoff bereitgestellt wird. Zu Beginn der Eisenverhüttung mit Steinkohlenkoks waren zur Gewinnung einer Tonne Roheisen etwa 8 t Koks oder etwa 5 t Holzkohle[121] erforderlich. Durch das um 1830 eingeführte Vorwärmen der Luft konnte der Koksverbrauch auf etwa 5 t pro Tonne Roheisen gesenkt werden. Um 1950 wurden in der Bundesrepublik Deutschland noch etwa 950 kg Koks pro Tonne Roheisen benötigt, was bis 1975 auf etwa 450 kg sank. In Japan wurde zu dieser Zeit der theoretische Mindestbedarf von 350–400 kg pro Tonne Roheisen fast erreicht.[122][123] Bei den Direktreduktionverfahren werden die Eisenerze, im Gegensatz zur Hochofenroute, „direkt“, also ohne Schmelzprozess und damit bei geringeren Temperaturen, zu festem Eisenschwamm reduziert, in dem die Begleitelemente der Erze noch enthalten sind. Im Verbund mit dem Einschmelzen des Eisenschwamms im Lichtbogenofen stellt die Direktreduktion eine energiesparendere Verfahrensalternative zur Hochofenroute dar.[124]
Eisenerzeugung im Hochofen

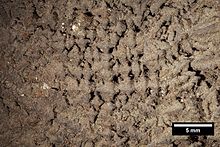
Das Eisen wird durch chemische Reduktion des Eisenoxids der oxidischen Eisenerze (oder sulfidischer Eisenerze nach ihrer Röstung mit Luftsauerstoff) und Kohlenstoff (Koks) gewonnen. Die Roheisenerzeugung erfolgt nahezu ausschließlich in hohen Gebläse-Schachtöfen (Hochöfen). Lediglich in Ländern mit billigen Wasserkraftwerken und teurer Kohle spielt die Erzeugung in elektrischen Öfen eine begrenzte Rolle. Koks und Erz werden im Hochofen abwechselnd in Lagen oben in den Ofen hineingeschüttet.[13] Dazu sind oberhalb des Ofengefäßes in der Regel zwei Bunker angeordnet, die als Gasschleusen zwischen dem Ofengefäß und der Umgebung dienen. Ganz oben befindet sich innerhalb des Ofengefäßes eine Drehschurre, mit der das Material spiralförmig flächig auf der Beschickungsoberfläche verteilt wird. Die Kokslagen halten im unteren Bereich des Ofens, wenn das Erz plastisch wird, die Durchströmbarkeit der Schüttung mit Prozessgas aufrecht (Koksfenster).[125]
Der Einsatz sinkt im Ofenschacht ab und wird dabei durch das etwa 1600 bis 2200 °C (an der Einblasstelle) heiße, aus Kohlenstoffmonoxid und Stickstoff bestehende aufsteigende Prozessgas getrocknet, aufgeheizt, die Eisenoxide reduziert und schließlich geschmolzen (Redoxreaktion). Das Prozessgas wird erzeugt, indem unten in den Ofen durch Blasformen (wassergekühlte Kupferdüsen[126]) auf etwa 900 bis 1300 °C vorgeheizte Luft eingeblasen wird. Der Sauerstoff der Luft verbrennt mit Koks zu Kohlenstoffmonoxid. Der gesamte Vorgang dauert etwa acht Stunden.[13]
In der Temperaturzone zwischen 500 und 900 °C findet die so genannte „Indirekte Reduktion“ statt. Über drei Stufen reagieren die verschiedenen Eisenoxide jeweils mit Kohlenstoffmonoxid oder Wasserstoff, bis schließlich metallisches Eisen vorliegt:[13]
oder
Aus Hämatit entsteht der stärker eisenhaltige Magnetit.
oder
Aus Magnetit entsteht Wüstit.
oder
Aus Wüstit entsteht metallisches Eisen, das sich unten im Hochofen ansammelt.
Im Temperaturbereich von 900 bis 1600 °C findet zusätzlich eine „direkte Reduktion“ mit Kohlenstoff statt:[13]
Das aus dem Hochofen kommende Gichtgas wird vom mitgeführten Staub befreit und dient zum Betrieb der für das Hochofenverfahren erforderlichen Winderhitzer, Gebläse, Pumpen, Beleuchtungs-, Gasreinigungs- und Transportvorrichtungen. Der Überschuss wird für den Stahlwerksbetrieb oder sonstige industrielle Zwecke verwendet.[13]
Der Ofen erzeugt neben dem flüssigen Eisen auch flüssige Schlacke. Da der Schmelzpunkt eines Gemisches von SiO2 und Al2O3 zu hoch ist, um eine bei 1450 °C flüssige Schlacke zu bilden, dienen Zuschläge der Erzeugung von leichter schmelzbaren Calcium-aluminium-silicate zur Schmelzpunktserniedrigung. Handelt es sich zum Beispiel um Tonerde- und Kieselsäure-haltige Gangarten, was meist der Fall ist, so werden dementsprechend kalkhaltige, das heißt basische Bestandteile (zum Beispiel Kalkstein, Dolomit) zugeschlagen. Im Falle kalkhaltiger Gangarten werden umgekehrt Tonerde- und Kieselsäure-haltige, das heißt saure Zuschläge (zum Beispiel Feldspat, Tonschiefer) zugegeben. Das Eisen und die Schlacke ist im Hochofen miteinander vermischt, hat eine Temperatur von etwa 1450 °C und wird durch ein Stichloch abgezogen, das etwa alle zwei Stunden durch Anbohren geöffnet und jeweils nach etwa einer Stunde durch Verstopfen mit einer keramischen Masse verschlossen wird. Eisen und Schlacke werden außerhalb des Ofens getrennt. Das Eisen wird in Transportpfannen gefüllt und ins Stahlwerk gebracht.[13][127]
Das Eisen ist bei 1450 °C flüssig, da durch den im Eisen gelösten Kohlenstoff eine Schmelzpunktserniedrigung erfolgt. Die Schlacke wird mit Wasser verdüst. Dabei erstarrt sie durch das Abschrecken als feinkörniges Glas (Schlackensand). Dieser Schlackensand wird fein gemahlen und als Betonzusatzstoff (Füller) verwendet. Im gesamten Herstellungsprozess entsteht je nach Verfahren im Hochofen pro Tonne Eisen zwischen 300[128] und 1000 kg Schlacke.[129]
Erz und Koks enthalten als Hauptverunreinigung Siliciumdioxid (Quarzsand, Silicate) SiO2 und Aluminiumoxid Al2O3. Ein kleiner Teil des Siliciumdioxids wird zu Silicium reduziert, das im Eisen gelöst wird. Der Rest bildet zusammen mit dem Aluminiumoxid die Schlacke (Calcium-Aluminiumsilikate[13]).
Das Eisen des Hochofens (Roheisen) hat nur einen Eisengehalt von etwa 95 %. Es enthält 0,5 bis 6 % Mangan, sowie für die meisten Anwendungen zu viel Kohlenstoff (2,5 bis 4 %), Schwefel (0,01 bis 0,05 %), Silicium (0,5 bis 3 %) und Phosphor (0 bis 2 %).[13] Üblicherweise wird daher im Stahlwerk zunächst durch Einblasen von Calciumcarbid, Magnesium oder Calciumoxid reduzierend entschwefelt, wobei eine optimale Entschwefelung vor allem eine Voraussetzung für die Herstellung von Gusseisen mit Kugelgraphit ist.[130] Kühlt Roheisen sehr langsam ab, zum Beispiel in Sandformen („Masselbetten“), so scheidet sich der gelöste Kohlenstoff als Graphit aus und „graues Roheisen“ (graue Bruchfläche, Schmelztemperatur etwa 1200 °C) wird erhalten. Mitbedingung dafür ist ein Überwiegen des Siliciumgehalts gegenüber dem Mangangehalt (> 2 % Si; <0,2 % Mn). Bei rascherer Abkühlung, zum Beispiel in Eisenschalen („Kokillen“), verbleibt der Kohlenstoff als Eisencarbid im Roheisen, so dass ein „weißes Roheisen“ (weißer Bruchfläche, Schmelztemperatur etwa 1100 °C, dient überwiegend zur Herstellung von Stahl) entsteht. Hier ist ein Überwiegen des Mangangehalts (< 0,5 % Si; > 4 % Mn) mitbedingend, der der Graphitausscheidung entgegenwirkt.[13]
Eisenerzeugung ohne Hochofen
Hochöfen haben einen großen Material- und Energiebedarf, der bei ungünstigen Rohstoff- und Energiebedingungen nicht immer bereitgestellt werden kann. Aufgrund dessen und wegen Umweltbelangen wurden alternative Verfahren zur Verarbeitung von Eisen entwickelt. Bei diesen sollen die vorhandenen Eisenerze ohne oder nur mit geringem Einsatz von Koks oder alternativ mit Steinkohle, Braunkohle, Erdöl oder Erdgas reduziert werden. Bei der überwiegenden Anzahl der als „Direkte Eisenreduktion“ bezeichneten Verfahren fällt das erzeugte Roheisen in fester, poriger Form an, das als Eisenschwamm oder „direktes“ Eisen bezeichnet wird und für die Stahlerzeugung geeignet ist.
Zwei Hauptreaktionen umfassen den direkten Reduktionsprozess: Bei der Verwendung von Methan (Erdgas) und Sauerstoff (alternativ Wasserdampf oder Kohlenstoffdioxid) wird dieses teilweise oxidiert (mit Wärme und einem Katalysator):[131]
Das Eisenerz wird dann in einem Ofen mit diesen Gasen behandelt, wobei fester Eisenschwamm entsteht:
Siliciumdioxid wird durch Zugabe eines Kalksteinflussmittels entfernt.[132]
Es gibt eine Reihe von bekannten Direktreduktionsverfahren. Diese unterscheiden sich unter anderem nach dem jeweiligen Reduktionsgefäß.[133]
Bei der Eisenerzeugung im Schachtofen wurde zuerst das Wiberg-Verfahren um 1918 in Schweden entwickelt. Später folgten das in den 1970er Jahren entwickelte Purofer-Verfahren in Oberhausen und das Midland-Ross-Verfahren/Midrex-Verfahren, das von der Midland-Ross-Corporation in Cleveland, Ohio entwickelt wurde. Allen drei Verfahren nutzen einen mehr oder weniger kurzen Schachtofen und als Einsatzstoffe eisenreiche Stückerze, Sinter oder Pellets, die vorgewärmt und am Ofenkopf eingebracht werden. Am Ofengrund wird ein 1000 °C heißes Reduktionsgasgemisch aus Kohlenstoffmonoxid (CO), Wasserstoff (H2), Kohlenstoffdioxid (CO2), Wasser (H2O) und ggf. Methan (CH4) eingeblasen.[134] Das Midrex-Verfahren ist auf einen externen Reformer angewiesen, in dem Methan in Wasserstoff und Kohlenstoffmonoxid umgewandelt wird. Das moderne Energiron-Verfahren (eine Weiterentwicklung vom HYL-Verfahren[135]) ist eine Gemeinschaftsentwicklung der italienischen Anlagenhersteller Tenova und Danieli. Bei Energiron-Verfahren gibt es keinen eigenen Reformer, sondern einen Prozessgaserhitzer. Die eigentliche Umwandlung des Erdgases findet nicht extern, sondern unter Druck (6–8 Bar) autokatalytisch direkt am Eisenerz im Schachtofen statt. Der dafür nötige Sauerstoff stammt aus dem Eisenerz.[136][137] Der erzeugte Eisenschwamm hat eine Reinheit von 85 bis 95 %. Eine leicht veränderte Variante ist das ab 1981 verwendete Corex-Verfahren.[134]
Für die Eisenerzeugung in der Retorte wurde 1908 von Sven Emil Sieurin in Höganäs Schweden das Höganäs-Verfahren und 1957 das HyL-Verfahren bei der Gesellschaft Hojalata-y-Lamina S.A. in Monterry, Mexiko entwickelt. Bei diesen werden sehr reiche Eisenerzkonzentrate in keramischen Retorten oder Muffeln eingebracht und entweder mit feinkörniger Kohle, Koksgrus und Kalkstein oder mit Erdgas reduziert. Der erzeugte Eisenschwamm hat eine Reinheit von 80 bis 95 % und wird entweder zur Herstellung von Sonderstählen oder als Eisenpulver für die Pulvermetallurgie genutzt.[134]
Bei der Eisenerzeugung in Drehgefäßen oder im Drehrohrofen kommen Verfahren wie das 1930 entwickelte Krupp-Rennverfahren oder Weiterentwicklungen wie das Krupp-Eisenschwammverfahren,[138] das 1964 von der Republic Steel Corporation und der National Lead Corporation gemeinsam mit der Steel Company of Canada und der Lurgi Gesellschaft für Chemie und Hüttenwesen entwickelte SL/RN-Verfahren zum Einsatz. Eingebracht werden hier Stückerz oder Pellets zusammen mit Kalkstein oder Dolomit in bis zu 110 m lange Drehrohröfen, die mit Braunkohle, Koksofengas oder Heizöl auf bis zu 1050 °C aufgeheizt werden. Erzeugt wird Eisenschwamm mit einer Reinheit von 85 bis über 90 %.[134] Eine Variante davon ist das bei der Stora Kopparbergs bergslag in Schweden entwickelte Dored-Verfahren (Domnarf-Reduktions-Verfahren). Bei diesem wird vorgewärmtes Eisenerz wird mit Kohle oder Koks auf einem Roheisensumpf in einen Drehrohrofen eingebracht. Durch Einblasen von reinem Sauerstoff wird das im Reduktionsgas enthaltene Kohlenstoffmonoxid zu Kohlenstoffdioxid verbrannt und der Drehrohrofen auf etwa 1300 bis 1350 °C aufgeheizt und so flüssiges Roheisen erzeugt.[139]
Bei der Eisenerzeugung im Wirbelschichtreaktor wird Eisenschwamm aus feinkörnigen Eisenerzen erzeugt, das entweder mit eingeblasenem Wasserstoff, Erdgas oder Raffinerierestgas aufgewirbelt und reduziert wird. Dafür kommen zum Beispiel das Finex-Verfahren, das von der Hydrocarbon Research Inc. (USA) entwickelte H-Iron-Verfahren oder das ab 1955 von der Esso Research & Engineering Company (einer Tochterfirma der Standard Oil Company), New York entwickelte FIOR-Verfahren (Fluid Iron Ore Reduction) zum Einsatz.[139][140]
Zur Eisenerzeugung im Elektroofen ohne Vorwärmung und Vorreduktion der Einsatzstoffe im Niederschachtofen kommen das 1925 entwickelte Tysland-Hole-Verfahren und das Demag-Verfahren zum Einsatz.[141] Das Elektrokemisk-Verfahren und Strategic-Udy-Verfahren benötigen dagegen die Vorwärmung und Vorreduktion des Erzes durch Drehrohröfen. Die Eisenerzeugung in Elektroöfen lohnt nur, wenn Strom in ausreichender Menge und kostengünstig bereitgestellt werden kann. Je nach Güte von Eisenerz und Kohlenstoffträger liegt der Energieverbrauch zwischen 2000 und 2500 kWh pro Tonne Roheisen.[139]
Weltweit sind nach dem Jahr 2000 nur das Midrex und Energiron-Direktreduktionverfahren von wirtschaftlicher Bedeutung.[142][137]
Thermitreaktion
Die Zündung eines Gemisches aus Aluminiumpulver und Eisen(III)-oxid liefert über die Thermitreaktion flüssiges metallisches Eisen:[143]
Die Reaktion hat zur Eisengewinnung aus Erz keine Bedeutung, unter anderem, weil das erforderliche Aluminium eine erhebliche Menge an Elektroenergie für seine Herstellung benötigt. Das aluminothermische Schweißen nutzt die bei der Reduktion des Eisenoxids mittels Aluminium übrigbleibende Energie des flüssigen Eisens zum Schmelzschweißen unter anderem von Eisenbahnschienen.[143]
Pyrophores Eisen
Pyrophores Eisen lässt sich durch thermisches Zersetzen von Eisen(II)-oxalat im Reagenzglas darstellen. Bringt man das abgekühlte Reaktionsgemisch mit Luft in Berührung, indem man es auf ein Stück Zunder gibt, entzünden sich die enthaltenen feinen Eisenpartikel und bringen den Zunder zum Glimmen.
Stahlproduktion
Im γ-Eisen ist Kohlenstoff bis maximal 2,06 % löslich, Stahl enthält 0 bis 2 % Kohlenstoff, er ist schmied- und walzbar, jedoch erst ab 0,5 % Kohlenstoff ist er härtbar. Liegt der Wert darunter, handelt es sich um nicht härtbaren Stahl oder Schmiedeeisen.[144]
Zur Stahlerzeugung wurden verschiedene Verfahren entwickelt, darunter Pfützenöfen, Bessemer-Konverter, Öfen mit offener Feuerstelle, Sauerstoffbasisöfen und Lichtbogenöfen. In allen Fällen besteht das Ziel darin, einen Teil oder den gesamten Kohlenstoff zusammen mit anderen Verunreinigungen zu oxidieren. Andererseits können andere Metalle zugesetzt werden, um legierte Stähle herzustellen.[13]
Je nach Verfahren wird dabei die eventuell entstandene Entschwefelungsschlacke abgezogen oder abgestochen und das Roheisen dann zur Herstellung von Stahl in einem Konverter (Sauerstoffblasverfahren, Windfrischverfahren wie das Thomas-Verfahren, Herdfrischverfahren wie das Siemens-Martin-Verfahren) unter Zusatz von Branntkalk und einblasen von Luft oder Sauerstoff oxidierend verblasen. Dabei wird Silicium zu Siliciumdioxid und Kohlenstoff zu Kohlenstoffdioxid verbrannt. Der Phosphor wird als Calciumphosphat gebunden. Das flüssige Eisen hat danach eine Temperatur von etwa 1600 °C. Es enthält soviel Sauerstoff, dass beim Erstarren aus verbliebenem Kohlenstoff Kohlenstoffmonoxidblasen entstehen. Beim meist verwendeten Stranggießen ist dies unerwünscht. Beim Abstechen des Stahls aus dem Konverter in die Gießpfanne wird daher Aluminium zugegeben, um den Sauerstoff als Aluminiumoxid zu binden. Bei hohen Anforderungen an die Qualität des Stahls folgen auf den Konverterprozess noch weitere Verfahrensschritte, wie eine Vakuumbehandlung (Sekundärmetallurgie).[13]
Alternativ kann Roheisen auch mit anderen Verfahren wie dem Puddelprozess oder Tempern sowie Schmiedeeisen (handelsübliches reines Eisen) durch Zementation zu Stahl (mit bis zu 2 % Kohlenstoff) verarbeitet werden.[13]
Eigenschaften
Physikalische Eigenschaften



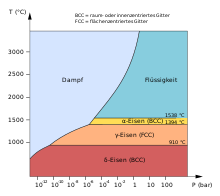

Chemisch reines Eisen ist ein silberweißes, verhältnismäßig weiches, dehnbares, recht reaktionsfreudiges Metall mit einer Dichte von 7,873 g/cm³, welches bei 1539 ± 1 °C schmilzt (hochreines Eisen in Helium bei Atmosphärendruck[11][12]) und bei 3070 °C siedet.[13] Technisch reines Eisen schmilzt bei 1534 ± 2 °C.[12] Der aus dem Dampfdruck berechnete Siedepunkt von hochreinem Eisen[145] wird bei technisch reinem Eisen mit 2860 °C deutlich niedriger angegeben,[146] wobei die in der Literatur angegebenen Werte teilweise deutlich voneinander abweichen.[147][148][8] Im Vakuum unterhalb eines Druckes von 10–5 mmHg sublimiert Eisen zwischen 1100 und 1200 °C.[147]
Das durchschnittliche Eisenatom hat etwa die 55-fache Masse eines Wasserstoffatoms. Der Atomkern des Eisenisotops 56Fe weist einen der größten Massendefekte und damit eine der höchsten Bindungsenergien pro Nukleon aller Atomkerne auf. Deshalb wird es als Endstufe bei der Energieerzeugung durch Kernfusion in den Sternen betrachtet. Den absolut höchsten Massendefekt hat jedoch 62Ni, gefolgt von 58Fe, und erst auf dem dritten Platz folgt 56Fe.[149][150]
Bei Raumtemperatur ist die einzig stabile allotrope Modifikation des reinen Eisens das Ferrit oder α-Eisen. Diese Modifikation kristallisiert in einer kubisch-raumzentrierten Kristallstruktur (Wolfram-Typ) in der Raumgruppe Im3m (Raumgruppen-Nr. 229) mit dem Gitterparameter a = 286,6 pm sowie zwei Formeleinheiten pro Elementarzelle. Diese Modifikation ist unterhalb von 910 °C stabil. Oberhalb dieser Temperatur wandelt es sich in die γ-Modifikation oder Austenit um. Diese besitzt eine kubisch-flächenzentrierte Struktur (Kupfer-Typ) mit der Raumgruppe Fm3m (Nr. 225) und dem Gitterparameter a = 364,7 pm.[151] Sie weist eine geringfügig höhere Dichte als α-Eisen auf.[152] Eine dritte Strukturänderung erfolgt bei 1390 °C, oberhalb dieser Temperatur bis zum Schmelzpunkt bei 1539 °C ist wieder das kubisch-raumzentrierte δ-Ferrit stabil.[151] Bei hohem Druck finden ebenfalls Phasenübergänge statt: bei Drücken von mehr als etwa 10 bis 15 GPa und Temperaturen von höchstens einigen hundert Grad Celsius wandelt sich α-Eisen in ε-Eisen, dessen Kristallgitter eine hexagonal dichteste Kugelpackung (hcp) ist, um; bei höheren Temperaturen bis hin zum Schmelzpunkt findet eine entsprechende Umwandlung von γ-Eisen zu ε-Eisen statt, wobei der Druck des Phasenübergangs mit der Temperatur steigt. Darüber hinaus gibt es möglicherweise einen weiteren Phasenübergang von ε-Eisen nach β-Eisen, der bei etwa 50 GPa und mehr als 1500 K liegt; die Existenz dieser β-Phase ist umstritten, und auch zu ihrer Kristallstruktur gibt es verschiedene Befunde, unter anderem eine orthorhombische oder eine doppelte hcp-Struktur.[153] Diese Umwandlungen wird die „Polymorphie des Eisens“ genannt.[6]
Das Fehlen einer β-Phase in der Standard-Nomenklatur der Eisenallotrope[154][155] rührt daher, dass früher angenommen wurde, dass die Änderung des Magnetismus am Curiepunkt bei 766 °C von Ferro- auf Paramagnetismus mit einer Strukturänderung einhergeht und somit eine weitere Modifikation zwischen 766 und 910 °C existiert, die als β-Modifikation oder β-Eisen bezeichnet wurde. Dies stellte sich jedoch nach genaueren Messungen als falsch heraus.[13]
Die Löslichkeit von Kohlenstoff in α-Eisen ist sehr gering und beträgt maximal 0,018 % bei 738 °C, wie aus dem Eisen-Kohlenstoff-Diagramm hervorgeht. Wesentlich mehr Kohlenstoff (bis zu 2,1 % bei 1153 °C) vermag sich in γ-Eisen zu lösen. In geschmolzenem Eisen beträgt die Löslichkeit von Kohlenstoff bei 1153 °C etwa 4,3 %, wobei diese mit steigender Temperatur noch zunimmt. Kühlt eine solche Eisenschmelze mit einem Kohlenstoffgehalt von über 4,3 % ab, scheidet sich aus ihr der überschüssige Kohlenstoff je nach Abkühlgeschwindigkeit als Graphit oder Zementit aus.[13]
Der Schmelzpunkt des Eisens ist experimentell nur für Drücke von bis zu etwa 50 GPa gut bestimmt. Bei höheren Drücken liefern verschiedene experimentelle Techniken stark unterschiedliche Ergebnisse. So lokalisieren verschiedene Studien den γ-ε-Tripelpunkt bei Drücken, die sich um mehrere Dutzend Gigapascal unterscheiden, und liegen bei den Schmelztemperaturen unter hohem Druck um 1000 K und mehr auseinander. Im Allgemeinen ergeben molekulardynamische Modellrechnungen und Schockexperimente höhere Temperaturen und steilere Schmelzkurven als statische Experimente in Diamantstempelzellen.[156]
Das Spektrum von Eisen zeigt Spektrallinien in allen Spektralbereichen.[157] In der Astronomie, genauer in der Röntgenastronomie, sind die im Röntgenbereich liegenden starken Emissionslinien von neutralem Eisen von großem Interesse. Astronomen beobachten sie in aktiven galaktischen Kernen, Röntgendoppelsternen, Supernovae und Schwarzen Löchern.[158]
Magnetische Eigenschaften

1. Stahlblech, 2. Elektroblech,
3. Gussstahl, 4. Wolframstahl,
5. Magnetstahl, 6. Gusseisen, 7. Nickel, 8. Cobalt, 9. Magnetit[159]
Als Übergangsmetall besitzt Eisen in jedem Atom ein permanentes magnetisches Moment.[160] Unterhalb seines Curie-Punktes von 770 °C wechselt α-Eisen von paramagnetisch zu ferromagnetisch: Die Spins der beiden ungepaarten Elektronen in jedem Atom richten sich im Allgemeinen nach den Spins seiner Nachbarn aus, wodurch ein magnetisches Gesamtfeld entsteht.[161] Dies geschieht, weil die Orbitale dieser beiden Elektronen (dz2 und dx2 − y2) nicht auf benachbarte Atome im Gitter zeigen und daher nicht an der Metallbindung beteiligt sind.[162]
In Abwesenheit einer externen Magnetfeldquelle werden die Atome spontan in magnetische Domänen mit einem Durchmesser von etwa 10 Mikrometern aufgeteilt.[163] Dies sind durch Blochwände begrenzte Kristallbereichen (Weissschen Bezirken). Wegen der regellosen Orientierung dieser magnetischen Domänen ist äußerlich kein Moment spürbar. Somit hat ein makroskopisches Stück reinen α-Eisens ein Gesamtmagnetfeld von nahezu Null.[160]
Eine andere Möglichkeit stellt die antiparallele Anordnung der Momente in Eisenlegierungen unterhalb der Néel-Temperatur TN dar (Antiferromagnetismus). Hier kompensieren sich die Momente bereits auf atomarer Ebene. Während im para- und antiferromagnetischen Zustand durch technisch übliche äußere Magnetfelder keine nennenswerte Polarisierung zu erreichen ist, gelingt dies im ferromagnetischen Zustand leicht durch Wanderung der Blochwände und Drehung der Polarisationsrichtung der Domänen.[160]
Das Anlegen eines externen Magnetfelds bewirkt, dass die Domänen, die in der gleichen allgemeinen Richtung magnetisiert sind, auf Kosten benachbarter Domänen wachsen, die in andere Richtungen weisen, wodurch das externe Feld verstärkt wird. Dieser Effekt wird in Elektrogeräten ausgenutzt, die Magnetfelder kanalisieren müssen, wie elektrischen Transformatoren, Magnetaufzeichnungsköpfen und Elektromotoren. Verunreinigungen, Gitterfehler oder Korn- und Partikelgrenzen können die Domänen an den neuen Positionen „fixieren“, so dass der Effekt auch nach dem Entfernen des äußeren Feldes bestehen bleibt und das Eisenobjekt somit zu einem Dauermagneten wird.[161] Dieser Magnetismus verliert sich bei reinem α-Eisens bei Entfernung des äußeren magnetischen Feldes wieder, ist also nur temporär. Dagegen besitzt kohlenstoffhaltiges Eisen, besonders Stahl, einen permanenten Magnetismus, der nach Entfernung des magnetischen Feldes erhalten bleibt.[13]
Ein ähnliches Verhalten zeigen einige Eisenverbindungen wie die Ferrite und das Mineral Magnetit, eine kristalline Form des gemischten Eisen(II,III)-oxids (obwohl der atomare Mechanismus, der Ferrimagnetismus, etwas anders ist). Magnetitstücke mit natürlicher Dauermagnetisierung (Magneteisensteine) waren die frühesten Kompasse für die Navigation. Magnetitteilchen wurden ausgiebig in magnetischen Aufzeichnungsmedien wie Kernspeichern, Magnetbändern, Disketten und Platten verwendet, bis sie durch Material auf Kobaltbasis ersetzt wurden.
Chemische Eigenschaften
Oxidationszustände von Eisen | ||
---|---|---|
Beispiele | Bemerkung | |
−2 | [Fe(CO)4]2−, [Fe(CO)2(NO)2] | |
−1 | [Fe2(CO)8]2− | |
0 | Fe(CO)5, Fe2(CO)9, Fe3(CO)12 | |
+1 | [Fe(H2O)5NO]2+ | äußerst ungewöhnlich. (Ringprobe, Nachweis von NO3−) |
+2 | FeCl2, FeSO4, FeO, Fe(OH)2, Ferrocen |
quasi-Abgabe der 4s-Elektronen |
+3 | FeCl3, Fe2O3, Fe(NO3)3, FeO(OH) | Hauptoxidationszahl, quasi-Abgabe der 4s-Elektronen und gleichmäßige Besetzung der 3d-Orbitale durch Abgabe eines 3d-Elektrons; diese Ionen sind fast farblos. |
+4 | Li2FeO3, BaFeO3 | kommt auch in den Katalysezyklen einiger Enzyme vor (z. B. Cytochrom-c-Oxidase, Cytochrom P450, Peroxidasen) |
+5 | FeO43− | |
+6 | K2FeO4, BaFeO4 | selten |
Eisen ist beständig an trockener Luft, in luft- und kohlenstoffdioxidfreiem Wasser, in Laugen,[13] in trockenem Chlor sowie in konzentrierter Schwefelsäure, konzentrierter Salpetersäure und basischen Agenzien (außer heißer Natronlauge) mit einem pH-Wert größer als 9. Diese Beständigkeit rührt von der Anwesenheit einer zusammenhängenden Oxid-Schutzhaut her. An Luft entsteht bei Raumtemperatur auf frisch poliertem Eisen in wenigen Minuten eine etwa 2 nm dicke Oxidschicht, die nach fünf Tagen auf etwa 6 nm angewachsen ist. Das Wachstum dieser Schichten erfolgt bei einigen Legierungen, wie auf chromhaltigen Stählen, sehr viel langsamer.[164] In nichtoxidierenden Säuren wie Salzsäure sowie verdünnter Schwefel- oder Salpetersäure löst sich Eisen rasch unter Entwicklung von Wasserstoff.[165][13]
Von Wasser wird es oberhalb von 500 °C, ebenso von heißen Laugen in umkehrbarer Reaktion zersetzt:[13]
Konzentrierte Natronlauge greift Eisen auch unter Luftabschluss an, dieses geht dabei unter Hydroxoferrat(II)-Bildung in Lösung. An feuchter Luft und in Wasser, das Sauerstoff oder Kohlenstoffdioxid enthält, wird Eisen leicht unter Bildung von Eisenoxidhydrat (Rosten) oxidiert. Da die dabei entstehende Oxidschicht weich und porös ist, kann der Rostvorgang ungehindert fortschreiten. Besonders aggressiv verhält sich elektrolythaltiges Meerwasser oder SO2-haltiges Wasser in Industriegebieten. Wird Eisen an trockener Luft erhitzt, so bildet sich eine dünne Schicht von Eisen(II,III)-oxid (Fe3O4, Eisenhammerschlag), die durch Dünnschichtinterferenz stark gefärbt erscheint (Anlassen). Bestimmte Temperaturen erzeugen spezifische Oxidschichtstärken und die Farbe kann zur Beurteilung der Anlasstemperatur verwendet werden.[166] Sehr fein verteiltes, pyrophores Eisen reagiert schon bei Raumtemperatur mit Sauerstoff aus der Luft unter Feuererscheinung. Brennende Stahlwolle reagiert in feuchtem Chlor-Gas kräftig unter Bildung von braunen Eisen(III)-chlorid-Dämpfen. Wird ein Gemisch aus Eisen- und Schwefelpulver (im Gewichtsverhältnis 7:4) erhitzt, so entsteht vorwiegend Eisen(II)-sulfid.[167] Mit weiteren Nichtmetallen wie Phosphor, Silicium, Schwefel und Kohlenstoff bildet Eisen bei erhöhter Temperatur jeweils Phosphide, Silicide, Sulfide oder Carbide.[165][13] Eisen bildet mit Wasserstoff keine unter Normalbedingungen stabilen binären Hydride, wirkt aber als Hydrierungskatalysator. Es bildet jedoch ternäre Hydride oder Donoraddukte.[13]
Geruch des Eisens
Reines Eisen ist geruchlos. Der typische, als metallisch klassifizierte Geruch, wenn Eisengegenstände berührt werden, entsteht durch eine chemische Reaktion von Stoffen des Schweißes und des Fetts der Haut mit den sich dabei bildenden zweiwertigen Eisenionen.[168]
Einer der wichtigsten Duftträger ist 1-Octen-3-on, das noch in großer Verdünnung pilzartig-metallisch riecht.[110] Dieser macht etwa ein Drittel des Geruchs aus. Der Rest sind andere Aldehyde und Ketone. Vorstufe der Geruchsstoffe sind Lipidperoxide.[169] Diese entstehen, wenn Hautfette durch bestimmte Enzyme oder nichtenzymatische Prozesse (zum Beispiel UV-Anteil des Lichts) oxidiert werden. Diese Lipidperoxide werden dann durch die zweiwertigen Eisenionen zersetzt, wobei die Duftstoffe gebildet werden. Die zweiwertigen Eisenionen entstehen durch Korrosion des Eisens bei Berührung mit dem Handschweiß, der korrosive organische Säuren und Chloride enthält.[169]
Beim Verreiben von Blut auf der Haut entsteht ein ähnlicher Geruch, da Blut ebenfalls Eisen(II)-ionen enthält und diese durch ähnliche Reaktionen Geruchsstoffe bilden.[169]
Von stark verrosteten Gegenständen (unter anderem Bildung von Eisen(III)-Verbindungen) geht bei Berührung kein metallischer Geruch aus, wie die Alltagserfahrung lehrt. In Übereinstimmung hiermit steht die Beobachtung, dass die Zersetzung von Lipidperoxiden nicht durch Eisen(III)-Ionen katalysiert wird.[169]
Gefahrstoffkennzeichnung
Sicherheitshinweise | |||||||
---|---|---|---|---|---|---|---|
Name |
Eisenpulver | ||||||
|
Während Eisen in massiver Form kein Gefahrstoff ist, können Eisenpulver brennbar, in feinst verteilter Form pyrophor sein. Entsprechend müssen solche Pulver mit einer zusätzlichen Gefahrstoffkennzeichnung versehen werden.[17]
Isotope
Eisen hat 27 Isotope und zwei Kernisomere, von denen vier natürlich vorkommende, stabile Isotope sind. Sie haben die relativen Häufigkeiten: 54Fe (5,8 %), 56Fe (91,7 %), 57Fe (2,2 %) und 58Fe (0,3 %). Das Isotop 60Fe hat eine Halbwertszeit von 2,62 Millionen Jahren,[15] 55Fe von 2,737 Jahren und das Isotop 59Fe eine von 44,495 Tagen.[170] Die restlichen Isotope und die beiden Kernisomere haben Halbwertszeiten zwischen weniger als 150 ns und 8,275 Stunden.[171] Die Existenz von 60Fe zu Beginn der Entstehung des Planetensystems konnte durch den Nachweis einer Korrelation zwischen den Häufigkeiten von 60Ni, dem Zerfallsprodukt von 60Fe, und den Häufigkeiten der stabilen Fe-Isotope in einigen Phasen mancher Meteorite (beispielsweise in den Meteoriten Semarkona und Chervony Kut[172]) nachgewiesen werden. Möglicherweise spielte die freigesetzte Energie beim radioaktiven Zerfall von 60Fe, neben der atomaren Zerfallsenergie des ebenfalls vorhandenen radioaktiven 26Al, eine Rolle beim Aufschmelzen und der Differenzierung der Asteroiden direkt nach ihrer Bildung vor etwa 4,6 Milliarden Jahren. Heute ist das ursprünglich vorhanden gewesene 60Fe in 60Ni zerfallen. Die Verteilung von Nickel- und Eisenisotopen in Meteoriten erlaubt es, die Isotopen- und Elementehäufigkeit bei der Bildung des Sonnensystems zu messen und die vor und während der Bildung des Sonnensystems vorherrschenden Bedingungen zu erschließen.[173][174] In Fossilien wurde 60Fe nachgewiesen, was darauf hindeutet, dass vor ca. 2,6 Millionen Jahren eine Supernovaexplosion in 150 Lichtjahren Entfernung stattgefunden hat, bei der dieses Nuklid erzeugt wurde.[175]
Von den stabilen Eisenisotopen besitzt nur 57Fe einen von null verschiedenen Kernspin. Es ist damit für die Mößbauerspektroskopie geeignet.[176]
Verwendung
Eisen ist mit 95 % Gewichtsanteil an genutzten Metallen das weltweit meistverwendete. Der Grund dafür liegt in seiner weiten Verfügbarkeit, welche es recht preiswert macht, und der hervorragenden Eigenschaften seiner Legierungen, die sie für viele Bereiche in der Technik zu einem Grundwerkstoff machen.[177]
Der größte Teil des aus Roheisen produzierten Eisens ist der Hauptbestandteil von Stahl und Gusseisen. Roheisen enthält vier bis fünf Prozent Kohlenstoff sowie unterschiedliche Anteile an Schwefel, Phosphor und Silicium. Es ist ein Zwischenprodukt in der Herstellung von Gusseisen und Stahl.[13] Gusseisen enthält über 2,06 % Kohlenstoff und weitere Legierungselemente, wie Silicium und Mangan, die die Gießbarkeit verbessern. Gusseisen ist sehr hart und spröde. Es lässt sich gewöhnlich nicht plastisch verformen (schmieden), aber sehr gut gießen wegen des vergleichsweise niedrigen Schmelzpunktes und der dünnflüssigen Schmelze.[178] Stahl enthält maximal 2,06 % Kohlenstoff. Im Gegensatz zu Gusseisen ist er schmiedbar. Durch Legieren, sowie eine geeignete Kombination von thermischer Behandlung (siehe Härten) und plastischer Formung (Kaltwalzen) können die mechanischen Eigenschaften des Stahls in weiten Grenzen variiert werden.[13] Stahl besitzt eine hervorragende Festigkeit und Zähigkeit beim Eingehen von Legierungen mit anderen Metallen wie Chrom, Molybdän und Nickel.[177] Es wird bei der Herstellung von Landfahrzeugen, Schiffen und im gesamten Baubereich (Stahlbetonbau, Stahlbau) eingesetzt. Weitere Einsatzgebiete sind Verpackungen (Dosen, Gebinde, Behälter, Eimer, Band), Rohrleitungen, Druckbehälter, Gasflaschen und Federn.[120] Industriell sind verschiedene Stähle verbreitet; in Deutschland sind etwa 7.500 Sorten genormt.[179]
Chemisch reines Eisen besitzt im Gegensatz zum kohlenstoffhaltigen Eisen nur eine untergeordnete technische Bedeutung. Es wird etwa als Material für Katalysatoren, wie dem Haber-Bosch-Verfahren in der Ammoniak-Synthese oder der Fischer-Tropsch-Synthese, genutzt.[13][180]
Eisen ist (neben Cobalt und Nickel) eines jener drei ferromagnetischen Metalle, die mit ihrer Eigenschaft den großtechnischen Einsatz des Elektromagnetismus unter anderem in Generatoren, Transformatoren, Drosseln, Relais und Elektromotoren ermöglichen.[139] Es wird rein oder unter anderem mit Silicium, Aluminium, Kobalt oder Nickel (siehe Mu-Metall) legiert und dient als weichmagnetisches Kernmaterial zur Führung von Magnetfeldern, zur Abschirmung von Magnetfeldern oder zur Erhöhung der Induktivität. Es wird hierzu massiv und in Form von Pulver (Pulverkerne), vor allem aber als Elektroblech produziert.[181][182]
Eisenpulver wird in der Chemie (zum Beispiel als Katalysator[180]) verwendet und dient in entsprechenden Tonband-Typen zur magnetischen Datenaufzeichnung. Eisendraht diente zur Datenaufzeichnung im Drahttongerät[183] und wird unter anderem zur Herstellung von Drahtseilen verwendet.
In der Medizin werden eisenhaltige Präparate als Antianämika eingesetzt, kausal in der Behandlung von Eisenmangelanämien und additiv in der Behandlung von durch andere Ursachen hervorgerufenen Anämien.[184] Viele Verbindungen des Eisens dienen als chemische Reagenzien und Pigmente (zum Beispiel Eisenoxidpigmente).[13]
Die Eigenschaft feiner Eisenspäne leicht Feuer zu fangen, wurde seit der Eisenzeit zum Schlagen von Funken mit dem Schlagfeuerzeug genutzt. Solche Feuerzeuge aus Feuerstahl, Feuerstein und Zunder waren in Europa und vielen anderen Regionen bis zur Einführung der Streichhölzer ab ca. 1830 die übliche Methode Feuer zu machen. Die steinzeitlichen Pyrit-Feuerzeuge verwenden eine Eisenverbindung, die sich unter Schlag entzündet: Eisen(II)-disulfid.[65]
Eisen wurde in der Alchemie verwendet, wo es mit dem Zeichen „♂“ für den Planeten Mars und für Männlichkeit assoziiert wurde.[185]
Biologische Bedeutung
Bestandteil von Lebewesen
Eisen ist ein essentielles Spurenelement für fast alle Lebewesen, bei Tieren vor allem für die Blutbildung.
In pflanzlichen Organismen beeinflusst es die Photosynthese sowie die Bildung von Chlorophyllen und Kohlenhydraten,[167] da in Pflanzen eisenhaltige Enzyme an der Photosynthese, der Chlorophyll- und Kohlenhydratbildung beteiligt sind. In Pflanzen kommt Eisen fast ausschließlich in Form von freien anorganischen Eisenionen vor. In der Nitrogenase (Stickstofffixierung) ist Eisen neben Molybdän ebenfalls enthalten. Es gibt Pflanzen, die aus kalkhaltigen Böden Eisenionen durch Phyto-Siderophore (eisenkomplexierende Verbindung) in Kombination mit lokaler Freisetzung von Wasserstoffionen bioverfügbar machen, dabei wird Fe3+ zu Fe2+ reduziert und anschließend komplexiert. In Pflanzen wird das Eisen, ähnlich wie in der Leber, an Phytoferritine gebunden. Bei Pflanzen ist es für die Chlorophyllsynthese unbedingt notwendig. Das Absinken des Eisen-Gehaltes in Pflanzen unter ein kritisches Minimum führt zum Erbleichen und Gelbwerden der grünen Pflanzenteile (Chlorose).[110]
In Pilzen (zum Beispiel als Ferrichrom, ein Siderophor mit wachstumsfördernden Eigenschaften), Bakterien (in Streptomyces wird das Ferrioxamin B gebildet) und Meereswürmern (in ihnen und in Lingula kommt das Nichthäm-Eisenprotein Hämerythrin vor) spielen Eisenverbindungen eine wichtige Rolle.[110]
Im Körper von Menschen und Tieren liegt es oxidiert als Eisen2+ und Eisen3+ vor. Als Zentralatom des Kofaktors Häm b in Hämoglobin, Myoglobin und Cytochromen ist es bei vielen Tieren und beim Menschen für Sauerstofftransport und -speicherung sowie für die Elektronenübertragung verantwortlich. In diesen Proteinen ist es von einem planaren Porphyrinring umgeben.[110]
Weiter ist Eisen Bestandteil von Eisen-Schwefel-Komplexen (so genannte Eisen-Schwefel-Cluster) in vielen Enzymen, beispielsweise Nitrogenasen, Hydrogenasen oder den Komplexen der Atmungskette. Als dritte wichtige Klasse der Eisenenzyme sind die so genannten Nicht-Häm-Eisenenzyme zu nennen, beispielsweise die Methan-Monooxygenase, Ribonukleotidreduktase und das Hämerythrin. Diese Proteine nehmen in verschiedenen Organismen Aufgaben wahr: Sauerstoffaktivierung, Sauerstofftransport, Redoxreaktionen und Hydrolysen.[110] Ebenso wichtig ist dreiwertiges Eisen als Zentralion im Enzym Katalase, das in den Peroxisomen der Zellen das im Stoffwechsel entstehende Zellgift Wasserstoffperoxid abbaut.[186] Eisenionen sind auch ein Katalysator bei der Oxidation organischer Verbindungen unter speziellen Bedingungen. Diese Fenton-Reaktion wird bei einem Überangebot an Eisen als eine der wesentlichen Quellen reaktiver Sauerstoffspezies in Zellen angesehen, welche eine Rolle bei verschiedenen Krankheiten und beim Altern spielen.[187][188]
Die Speicherung des Eisens erfolgt intrazellulär in dem Enzym Ferritin (20 % Eisenanteil) und dessen Abbauprodukt Hämosiderin (37 % Eisenanteil). Transportiert wird Eisen durch Transferrin.[189]
Der Mensch enthält 2,5 bis 4 g Eisen, davon finden sich 60 % (2,0 bis 2,5 g) im Hämoglobin der Erythrocyten, etwa 1 g in Leber und Knochenmark (Speicherproteine Ferritin und Hämosiderin), etwa 10 % bis 15 % im Myoglobin (etwa 400 mg Eisen), 250 mg in Enzymsystemen 0,1 bis 0,2 % Eisen in Transportproteinen (zum Beispiel Schwefel-, Eisenproteine, Cytochrome) (Cytochrom: 0,1 % des Gesamteisens).[110]
Externer Elektronendonor und -akzeptor
Einige Bakterien nutzen Fe(III) als Elektronenakzeptor für die Atmungskette. Sie reduzieren es damit zu Fe(II), was eine Mobilisierung von Eisen bedeutet, da die meisten Fe(III)-Verbindungen schwer wasserlöslich sind, die meisten Fe(II)-Verbindungen aber gut wasserlöslich. Einige phototrophe Bakterien nutzen Fe(II) als Elektronendonator für die Reduktion von CO2.[190]
Medizinische Bedeutung
Eisenbedarf und Eisenmangel
Eisen ist in der Oxidationsstufe Fe2+ und Fe3+ essenziell für alle Organismen. Der tägliche Bedarf beträgt für Männer 1 mg, für Frauen 2 mg. Aufgrund der ineffizienten Resorption muss die Zufuhr über die Nahrung bei Männern etwa 5 bis 9 mg und bei Frauen 14 bis 18 mg betragen. Ein Eisenmangel kann am ehesten bei Schwangeren und Sportlern auftreten. Aus der Muttermilch kann ein Säugling etwa 50 % des Eisens resorbieren, aus der Kuhmilch nur 20 %.[110]
Vor allem Frauen vor den Wechseljahren können einen Eisenmangel aufweisen; ein Grund dafür ist der erhöhte Bedarf aufgrund der Menstruation. In Deutschland ist eine Unterversorgung auf 2 % bei erwachsenen Männern beziehungsweise und 5 % der Frauen geschätzt worden.[191] Frauen sollten circa 15 Milligramm Eisen pro Tag zuführen, während der Tagesbedarf eines erwachsenen Mannes nur etwa 10 Milligramm beträgt. Außerdem verlieren Frauen zusätzlich bei der Geburt eines Kindes circa 1000 Milligramm Eisen. Durch die gleichzeitige Einnahme von Vitamin C wird die Resorptionsquote von Eisen deutlich erhöht. Besonders reichhaltig ist Eisen in Blutwurst, Leber, Hülsenfrüchten und Vollkornbrot enthalten und nur gering in (Muskel-)Fleisch. Gleichzeitiger Verzehr von Milchprodukten, Kaffee oder schwarzem Tee hemmt jedoch die Eisenaufnahme.[192][193]
Toxizität und Eisenüberladung
Menschen
Eisen ist ein wichtiges Spurenelement für den Menschen, kann jedoch bei Überdosierung schädlich wirken.[194][195][196] Davon sind vor allem Menschen betroffen, die an Hämochromatose, einer Regulationsstörung der Eisenaufnahme im Darm, leiden. Das Eisen reichert sich im Verlauf der Krankheit in der Leber an und führt dort zu einer Siderose und weiteren Organschäden.[110]
Weiterhin steht Eisen im Verdacht, Infektionskrankheiten, zum Beispiel Tuberkulose zu fördern, da die Erreger zur Vermehrung ebenfalls Eisen benötigen.[197] Eine Überversorgung an Eisen führt zur erhöhten Anfälligkeit gegenüber Infektionskrankheiten (Tuberkulose, Salmonellose, AIDS, Yersiniose).[110] Außerdem kommt es bei einigen neurodegenerativen Erkrankungen wie der Parkinson- oder der Alzheimer-Krankheit zu Eisenablagerungen in bestimmten Bereichen des Gehirns. Im Jahr 2014 war noch unklar, ob dies eine Ursache oder eine Folge der Erkrankung ist.[198]
Risikogruppen für eine Unterversorgung sind Kinder und Jugendliche in der Wachstumsphase sowie Schwangere und Stillende. Einige andere Bevölkerungsgruppen nehmen hingegen viel mehr Eisen auf, als für die Bedarfsdeckung notwendig wäre. Daher sind Eisenpräparate oder andere eisenhaltige Nahrungsergänzungsmittel nur zu empfehlen, wenn ein ärztlich diagnostizierter Eisenmangel vorliegt.[199]
Pflanzen
In pflanzlichen Organismen ist Eisen ein essentielles Spurenelement. Es beeinflusst die Photosynthese sowie die Bildung von Chlorophyll und Kohlenhydraten.[167] Eisenüberladung kann sich jedoch in Form von Eisentoxizität bemerkbar machen. In Böden liegt es bei normalen pH-Werten als Fe(OH)3 vor. Bei geringem Sauerstoffgehalt des Bodens wird Eisen(III) durch Reduktion zum Eisen(II) reduziert. Dadurch wird das Eisen in eine lösliche, für Pflanzen verfügbare Form gebracht. Nimmt diese Verfügbarkeit unter anaeroben Bedingungen, zum Beispiel durch Bodenverdichtung, zu stark zu, können Pflanzenschäden durch Eisentoxizität auftreten, eine Erscheinung, die besonders in Reisanbaugebieten bekannt ist.[200]
Nachweis

Für Eisen existieren eine Reihe von Nachweismethoden. Neben spektralanalytischen Verfahren (Eisen liefert ein linienreiches Spektrum) sind vielfältige chemische Nachweisverfahren bekannt. Bei der Nachweisreaktion für Eisen-Ionen werden zunächst die beiden Kationen Fe2+ und Fe3+ unterschieden.[201]
Eisennachweis mit Thioglycolsäure
Mit Thioglycolsäure lassen sich Fe2+- und Fe3+-Ionen nachweisen:[139]
Die erste Reaktion findet nur bei Anwesenheit von Fe3+-Ionen statt.[202] Bei Anwesenheit von Fe2+- oder Fe3+-Ionen entsteht eine intensive Rotfärbung.
Eisennachweis mit Hexacyanoferraten
Die Fe2+-Ionen lassen sich mit rotem Blutlaugensalz nachweisen:
Fe3+-Ionen lassen sich mit gelbem Blutlaugensalz nachweisen:
Bei beiden Nachweisreaktionen entsteht tiefblaues Berliner Blau, ein wichtiger Farbstoff. Es läuft keine Komplexbildungsreaktion ab, sondern lediglich ein Kationenaustausch.
Beide Pigmente sind weitgehend identisch, da zwischen ihnen ein chemisches Gleichgewicht besteht. Dabei geht Fe3+ in Fe2+ über und umgekehrt:[203][204][205]
Die besonders intensive blaue Farbe des Komplexes entsteht durch Metall-Metall-Charge-Transfers zwischen den Eisen-Ionen. Es ist bemerkenswert, dass dieses bekannte Eisennachweisreagenz selbst Eisen enthält, welches durch die Cyanidionen chemisch gut maskiert wird (Innerorbitalkomplex) und somit die Grenzen der chemischen Analytik aufzeigt.
Eisennachweis mit Thiocyanaten
Alternativ kann Eisen(III)-salze mit Thiocyanaten (Rhodaniden) nachgewiesen werden. Diese reagieren mit Eisen(III)-Ionen zu Eisen(III)-thiocyanat:[206]
Es bildet sich das tiefrote Eisen(III)-thiocyanat (Fe(SCN)3), welches in Lösung bleibt. Einige Begleitionen stören diesen Nachweis (zum Beispiel Co2+, Mo3+, Hg2+, Überschuss an Mineralsäuren), so dass unter Umständen ein Kationentrennungsgang durchgeführt werden muss.
Eisennachweis mit Dimethylglyoxim
Eisen(II)-Ionen bilden mit Dimethylglyoxim einen planaren Komplex. Dazu wird zu einer (mit Weinsäure versetzte, ammoniakalisch gemachten) zu prüfenden Lösung einige Tropfen einer 1 %igen alkoholischen Dimethylglyoximlösung zugesetzt. Es bildet sich der intensiv rote Eisen(II)-Komplex. Die zugesetzte Weinsäure verhindert die Fällung von Eisenhydroxiden, sodass der sehr empfindliche Nachweis auch bei Anwesenheit von Fe(III)-Ionen ausführbar ist.[206]
Eisennachweis mit 2,2′-Bipyridin- oder 1,10-Phenanthrolin
Eisen(II)-Ionen bilden mit 2,2′-Bipyridin oder 1,10-Phenanthrolin in schwach saurer, neutraler oder ammoniakalischer Lösung rote Chelatkomplexe. Zum Nachweis von Eisen(III)-Ionen müssen diese vorher (zum Beispiel mit Hydroxylaminhydrochlorid) zu Eisen(II)-Ionen reduziert werden.[206]
Verbindungen
In seinen chemischen Verbindungen tritt Eisen hauptsächlich mit den Oxidationsstufen +2 (zum Beispiel Eisen(II)-chlorid), +3 (zum Beispiel Eisen(III)-fluorid), ferner +6 (zum Beispiel Bariumferrat(VI)) auf, doch existieren auch Verbindungen mit den Oxidationsstufen -2, -1 und 0 (zum Beispiel Eisenpentacarbonyl) sowie +1, +4 und +5. In keiner Verbindung tritt das Eisen in der seiner Nebengruppennummer VIII entsprechenden Oxidationsstufe auf. Seit 2016 sind Eisenverbindungen in der Oxidationsstufe +7 bekannt.[207]
Oxide


Eisen bildet mit Sauerstoff zweiwertige und dreiwertige Oxide. Da diese keine feste Schutzschicht bilden, oxidiert ein der Atmosphäre ausgesetzter Eisenkörper vollständig. Die poröse Oxidschicht verlangsamt den Oxidationsvorgang, kann ihn jedoch nicht verhindern, weshalb das Brünieren als schwacher Schutz vor Korrosion dient.[208] Wenn Eisenkörper vor dem endgültigen Verrosten eingesammelt und dem Recycling zugeführt werden, sind verrostetes Eisen und verrosteter Stahl bei der Stahlerzeugung im Elektro-Schmelzofen ein begehrter und wertvoller Sauerstoffträger. Dieser Sauerstoff im Eisenschrott wirkt beim „Stahlkochen“ als Oxidationsmittel, um ungewünschte qualitätsmindernde Beimengungen (zum Beispiel Leichtmetalle) zu oxidieren.
Eisen(III)-oxid (Fe2O3) ist eine rote bis braune Substanz und entsteht durch Oxidation von Eisen im Sauerstoffüberschuss. In der Natur tritt es in Form der Minerale Hämatit und Maghemit auf. Eisen(II,III)-oxid (Fe3O4) entsteht auf natürlichem Wege durch vulkanische Vorgänge oder beim direkten Verbrennen von Eisen, zum Beispiel mit dem Schneidbrenner als Eisenhammerschlag und wird als Mineral als Magnetit bezeichnet. Eisen(II)-oxid (FeO) entsteht bei der Zersetzung von Eisen(II)-oxalat FeC2O4 bei 850 °C im Vakuum. Es ist schwarz und bis 560 °C instabil. Als Mineral Wüstit entsteht es meist aus der Umwandlung von Magnetit bei hohen Temperaturen. Daneben ist mit FeO2 noch ein weiteres Eisenoxid bekannt.[209]
Eisen(III)-hydroxidoxid (FeO(OH)) gehört zur Gruppe der Eisenhydroxide oder Eisen(III)-oxidhydrate, die sich im Grad ihrer Hydratation unterscheiden. Beim Erwärmen geht Eisen(III)-hydroxidoxid in Eisen(III)-oxid über. Die α-Form kommt in der Natur als Nadeleisenerz oder Goethit vor. Die y-Form kommt in der Natur als Rubinglimmer oder Lepidokrokit vor. In der α-Form hat es eine orthorhombische Kristallstruktur, Raumgruppe Pbnm (Raumgruppen-Nr. 62, Stellung 3) .[210]
Eisenoxide und Eisenhydroxide werden als Lebensmittelzusatzstoffe verwendet (E 172).
Salze
Eisen bildet zweiwertige und dreiwertige Salze.
Eisen(II)-chlorid (FeCl2 · 6 H2O) wird zum Ausfällen von Sulfiden, Faulgasentschwefelung, Biogasentschwefelung, Chromatreduzierung und Phosphorelimination verwendet; dazu gehört die Simultanfällung. Es besitzt eine Kristallstruktur vom Cadmium(II)-chlorid-Typ mit der Raumgruppe R3m (Raumgruppen-Nr. 166) . Eisen(II)-fluorid ist in reinem Zustand ein weißer Feststoff, welcher in Wasser wenig löslich ist. Es besitzt eine Kristallstruktur vom Rutil-Typ, Raumgruppe P42/mnm (Raumgruppen-Nr. 136) . Eisen(II)-bromid und Eisen(II)-iodid sind kristalline, hygroskopische Feststoffe, die eine trigonale Kristallstruktur vom Cadmium(II)-hydroxid-Typ mit der Raumgruppe P3m1 (Raumgruppen-Nr. 164) haben. Eisen(II)-sulfat (FeSO4 · 7 H2O) wird wegen seiner Farbe auch Grünsalz genannt, als Mineral Melanterit. Es wird wie Eisen(II)-chlorid verwendet, sowie bei getrocknetem Eisen(II)-sulfat als Chromatreduzierer speziell im Zement gegen die Chromatallergie.
Wasserfreies Eisen(III)-chlorid (FeCl3 · 6 H2O) ist eine schwarze, leicht stechend nach Salzsäure riechende Substanz. Als wasserfreie Verbindung ist es extrem hygroskopisch, entzieht also der Luft Wasser. Mit steigendem Wassergehalt nimmt die hygroskopische Natur ab und die Farbe verändert sich über rot-bräunlich bis hin zu gelblich. Eisen(III)-chlorid hat eine trigonale Kristallstruktur mit der Raumgruppe R3 (Raumgruppen-Nr. 148) . Es kann Kupfer oxidieren und lösen. Deshalb können wässrige Eisen(III)-chlorid-Lösungen zum schonenden Ätzen von Leiterplatten verwendet werden.
Eisen(III)-nitrat wird zum Gerben verwendet. In der Textilindustrie wird es als Beize für Baumwollstoffe und zum Schwarzfärben von Seide durch Abscheiden von Eisen(III)-hydroxid verwendet. Weiterhin wird es seit langem als Korrosionsinhibitor verwendet. In neuerer Zeit wird es, nicht immer erfolgreich, zur Reduktion der Schwefelwasserstoffkonzentration in druckführenden Abwasserleitungen verwendet. Eisen(III)-sulfat wird in Großkläranlagen zur Desodorierung und zur Ausfällung von Phosphaten (unter anderem bei der Wasseraufbereitung und der Industriewasserentsorgung) sowie in der Metallurgie als Beizmittel (zum Beispiel für Aluminium und Stahl) eingesetzt.[211] In der Medizin ist eine blutstillende und adstringierende Wirkung bekannt.
Viele Eisensalze, wie zum Beispiel Eisen(III)-chloridsulfat (FeClSO4), werden unter anderem als Flockungsmittel und zur Phosphorelimination verwendet. Dazu gehören die Vorfällung, Simultanfällung, Nachfällung und Flockenfiltration sowie das Ausfällen von Sulfiden, Faulgasentschwefelung und Biogasentschwefelung.
Weitere Eisenverbindungen

Daneben sind viel weitere Eisenverbindungen bekannt.
So tritt das Zementit genannte Eisencarbid (Fe3C) als metastabile Phase in Stahl und weißem Gusseisen auf. Eisenpentacarbonyl (Fe(CO)5), auch IPC (von en: iron pentacarbonyl) genannt, entsteht unter Druck aus Eisen und Kohlenstoffmonoxid und bildet nach seiner Zersetzung neben Kohlenstoffmonoxid ein besonders reines Eisenpulver, das Carbonyleisen. Weitere Eisencarbonyle sind Dieisennonacarbonyl Fe2(CO)9 und Trieisendodecacarbonyl Fe3(CO)12. Ferrocen (Fe(C5H5)2) ist eine (Sandwichverbindung) aus der Stoffgruppe der Metallocene, dessen Derivate vielseitige Anwendungen im Bereich der Sensorik, der Katalyse und der Medizin finden.
Berliner Blau (Fe4[Fe(CN)6]3) ist ein lichtechtes, tiefblaues, anorganisches Pigment. Es wird aus einer Lösung von Eisen(III)-Salz und gelbem Blutlaugensalz hergestellt und findet Verwendung als Anstrichmittel und zum Tapetendruck sowie als Gegenmittel bei Vergiftungen mit radioaktiven Isotopen von Caesium oder mit Thallium. Es wird aufgrund seines feinen Korns und der daraus resultierenden Lasierfähigkeit sowie seiner großen Farbstärke für Aquarell-, Öl- und Druckfarben verwendet.[212]
Literatur
- Wilhelm Baer: Das Eisen : Seine Geschichte, Gewinnung und Verarbeitung. Handbuch für Eisengießer, Maschinenbauen, Gewerbtreibende, Fabrikanten und Bauherren. Leipzig 1862 (Digitalisat)
- Ludwig Beck: Die Geschichte des Eisens in technischer und kulturgeschichtlicher Beziehung. Band 1–5, Vieweg, Braunschweig 1884–1903.
- Harry H. Binder: Lexikon der chemischen Elemente – das Periodensystem in Fakten, Zahlen und Daten. S. Hirzel Verlag, Stuttgart 1999, ISBN 3-7776-0736-3.
- Vagn Fabritius Buchwald: Iron and steel in ancient times. Kong. Danske Videnskab. Selskab, Kopenhagen 2005, ISBN 87-7304-308-7.
- A. F. Holleman, E. Wiberg, N. Wiberg: Lehrbuch der Anorganischen Chemie. 102. Auflage. Walter de Gruyter, Berlin 2007, ISBN 978-3-11-017770-1, S. 1636–1666.
- Otto Johannsen (im Auftrag des Vereins Deutscher Eisenhüttenleute): Geschichte des Eisens. 3. Auflage. Verlag Stahleisen, Düsseldorf, 1953.
- Otto Johannsen: Geschichte des Eisens. Düsseldorf 1925 (Digitalisat)
- Hans Schoppa: Was der Hochöfner von seiner Arbeit wissen muss. Verlag Stahleisen, Düsseldorf 1992, ISBN 3-514-00443-9.
- Verein Deutscher Eisenhüttenleute: Gemeinfassliche Darstellung des Eisenhüttenwesens. 17. Auflage. Stahleisen, Düsseldorf 1970/71.
Weblinks
- Literatur von und über Eisen im Katalog der Deutschen Nationalbibliothek
- Mineralienatlas:Eisen im Mineralienatlas
- Mineralienatlas:Mineralienportrait/Eisen im Mineralienatlas
- Eisenherstellung in der Römerzeit bei die-roemer-online.de
- Eisengewinnung in vorgeschichtlicher Zeit auf der Internetpräsenz vom Landschaftsmuseum Obermain
Einzelnachweise
- ↑ a b c Harry H. Binder: Lexikon der chemischen Elemente. S. Hirzel Verlag, Stuttgart 1999, ISBN 3-7776-0736-3.
- ↑ Die Werte für die Eigenschaften (Infobox) sind, wenn nicht anders angegeben, aus www.webelements.com (Eisen) entnommen.
- ↑ CIAAW, Standard Atomic Weights Revised 2013.
- ↑ a b c d e Eintrag zu iron in Kramida, A., Ralchenko, Yu., Reader, J. und NIST ASD Team (2019): NIST Atomic Spectra Database (ver. 5.7.1). Hrsg.: NIST, Gaithersburg, MD. doi:10.18434/T4W30F (physics.nist.gov/asd). Abgerufen am 11. Juni 2020.
- ↑ a b c d e Eintrag zu iron bei WebElements, www.webelements.com, abgerufen am 11. Juni 2020.
- ↑ a b K. Schubert: Ein Modell für die Kristallstrukturen der chemischen Elemente. In: Acta Crystallographica. 1974, B30, S. 193–204 (doi:10.1107/S0567740874002469).
- ↑ a b Martin Okrusch, Siegfried Matthes: Mineralogie: Eine Einführung in die spezielle Mineralogie, Petrologie und Lagerstättenkunde. 7. Auflage. Springer Verlag, Berlin / Heidelberg / New York 2005, ISBN 3-540-23812-3, S. 22.
- ↑ a b Yiming Zhang, Julian R. G. Evans, Shoufeng Yang: Corrected Values for Boiling Points and Enthalpies of Vaporization of Elements in Handbooks. In: Journal of Chemical & Engineering Data. Band 56, 2011, S. 328–337 (doi:10.1021/je1011086).
- ↑ Ludwig Bergmann, Clemens Schaefer, Rainer Kassing: Lehrbuch der Experimentalphysik, Band 6: Festkörper. 2. Auflage. Walter de Gruyter, 2005, ISBN 3-11-017485-5, S. 361.
- ↑ Jan Hoinkis: Chemie für Ingenieure. John Wiley & Sons, 2015, ISBN 978-3-527-68456-4, S. 162.
- ↑ a b L. J. Swartzendruber: The Fe (Iron) system. In: Bulletin of Alloy Phase Diagrams. Band 3, Nr. 2, 1982, S. 161–165, doi:10.1007/BF02892374.
- ↑ a b c W.F. Roeser, H.T. Wensel: Freezing temperatures of high-purity iron and of some steels. In: Journal of Research of the National Bureau of Standards. Band 26, Nr. 4, 1941, S. 273, doi:10.6028/jres.026.015.
- ↑ a b c d e f g h i j k l m n o p q r s t u v w x y z A. F. Holleman, E. Wiberg, N. Wiberg: Lehrbuch der Anorganischen Chemie. 102. Auflage. Walter de Gruyter, Berlin 2007, ISBN 978-3-11-017770-1, S. 1637–1642.
- ↑ S. L. Keshava, K. Gopala, P. Venkataramaiah: Decay energy of 55Fe from its inner bremsstrahlung spectrum. In: Pramana. Band 56, Nr. 6, 2001, S. 735–744, doi:10.1007/s12043-001-0074-0.
- ↑ a b G. Rugel, T. Faestermann, K. Knie, G. Korschinek, M. Poutivtsev, D. Schumann, N. Kivel, I. Günther-Leopold, R. Weinreich, M. Wohlmuther: New Measurement of the 60Fe Half-Life. In: Physical Review Letters. 103, 2009, S. 072502, doi:10.1103/PhysRevLett.103.072502.
- ↑ Graham A. Webb: Annual Reports on NMR Spectroscopy. Elsevier Science, 2022, ISBN 978-0-323-98874-2, S. 188 (eingeschränkte Vorschau in der Google-Buchsuche).
- ↑ a b c d Eintrag zu Eisen, Pulver in der GESTIS-Stoffdatenbank des IFA, abgerufen am 3. Januar 2023. (JavaScript erforderlich)
- ↑ Dieses Element in massiver Form ist nach GESTIS, Abschnitt „Chemische Eigenschaften“ nicht als Gefahrstoff eingestuft.
- ↑ a b c Das Wort für 'Eisen' im Keltischen und Germanischen und die indogermanischen -erno-Bildungen | Jón Axel Harðarson, Academia.edu, aus Das Nomen im Indogermanischen, ISBN 978-3-95490-025-1, abgerufen am 28. Dezember 2022
- ↑ Julius Pokorny: Herkunft und Etymologie des Wortes Eisen. In: Zeitschrift für vergleichende Sprachforschung. Band 46, 1914, S. 128–150.
- ↑ Friedrich Kluge: Etymologisches Wörterbuch der deutschen Sprache. 25. Auflage. De Gruyter, 2012, ISBN 978-3-11-022365-1, S. 173 (eingeschränkte Vorschau in der Google-Buchsuche).
- ↑ Heinrich Beck, Johannes Hoops: Reallexikon der Germanischen Altertumskunde. W. de Gruyter, 1989, ISBN 3-11-011445-3, S. 59 (eingeschränkte Vorschau in der Google-Buchsuche).
- ↑ Jochen Stark, Bernd Wicht: Geschichte der Baustoffe. Vieweg Teubner Verlag, 2013, ISBN 978-3-322-92892-4, S. 106 (eingeschränkte Vorschau in der Google-Buchsuche).
- ↑ a b c d e f g h i j k l m n o Florian Neukirchen: Von der Kupfersteinzeit zu den Seltenen Erden – Eine kurze Geschichte der Metalle. Springer-Verlag, 2016, ISBN 978-3-662-49347-2, S. 65 (eingeschränkte Vorschau in der Google-Buchsuche).
- ↑ a b H. Moesta: Erze und Metalle. Springer Berlin Heidelberg, 2013, ISBN 978-3-540-16561-3, S. 152 (eingeschränkte Vorschau in der Google-Buchsuche).
- ↑ Vagn Fabritius Buchwald: Iron and Steel in Ancient Times. The Royal danish academy of sciences and letters, 2005, ISBN 87-7304-308-7, S. 72 (eingeschränkte Vorschau in der Google-Buchsuche).
- ↑ Otto Johannsen: Geschichte des Eisens. 3. Auflage. Stahleisen, Düsseldorf 1953, ISBN 3-514-00002-6, S. 6.
- ↑ a b Otto Johannsen: Geschichte des Eisens. 3. Auflage. Stahleisen, Düsseldorf 1953, ISBN 3-514-00002-6, S. 38.
- ↑ Thilo Rehren, Tamas Belgya, Albert Jambon, György Káli, Zs Kasztovszky, Zoltan Kis, Imre Kovács, Boglarka Maróti, Marcos Martinon-Torres, Gianluca Miniaci, Vincent Pigott, Miljana Radivojević, L. Rosta, László Szentmiklósi, Z. Szőkefalvi-Nagy: 5,000 years old Egyptian iron beads made from hammered meteoritic iron. In: Journal of Archaeological Science. Band 40, 2013, S. 4785–4792. doi:10.1016/j.jas.2013.06.002.
- ↑ Daniela Comelli, Massimo D’orazio, Luigi Folco, Mahmud El-Halwagy, Tommaso Frizzi, Roberto Alberti, Valentina Capogrosso, Abdelrazek Elnaggar, Hala Hassan, Austin Nevin, Franco Porcelli, Mohamed G. Rashed, Gianluca Valentini: The meteoritic origin of Tutankhamun’s iron dagger blade. In: Meteoritics & Planetary Science. Band 51, Nr. 7, Juli 2016, S. 1301–1309, doi:10.1111/maps.12664.
- ↑ a b Otto Johannsen: Geschichte des Eisens. 3. Auflage. Stahleisen, Düsseldorf 1953, ISBN 3-514-00002-6, S. 40.
- ↑ Otto Johannsen: Geschichte des Eisens. 3. Auflage. Stahleisen, Düsseldorf 1953, ISBN 3-514-00002-6, S. 44.
- ↑ Jörg Klinger, J. David Hawkins: Herrscherinschriften und andere Dokumente zur politischen Geschichte des Hethiterreiches. Gütersloher Verlagshaus, 2005, ISBN 3-641-21988-4, doi:10.14315/9783641219888-006/html.
- ↑ Friedrich Cornelius: Grundzüge der Geschichte der Hethiter 5. Auflage, WBG (Wissenschaftliche Buchgesellschaft), 1992, 382 S., ISBN 978-3-534-06190-7.
- ↑ Ünsal Yalcin: Zum Eisen der Hethiter. In: Das Schiff von Uluburun. 2005 (academia.edu).
- ↑ a b Charles Burney: Historical Dictionary of the Hittites. Historical Dictionaries of Ancient Civilizations and Historical Eras. Scarecrow Press, 2004, ISBN 0-8108-6564-5, S. 135–136.
- ↑ Richard A. Gabriel: The Great Armies of Antiquity. Greenwood Publishing Group, 2002, ISBN 0-275-97809-5, S. 75.
- ↑ Wolfgang Helck: Eisen. In: Wolfgang Helck, Eberhard Otto (Hrsg.): Lexikon der Ägyptologie. Band 1, Harrassowitz, Wiesbaden 1975, Spalte 1209–1210.
- ↑ Howard Vyse: Operations carried on at the Pyramids of Gizeh in 1837. Band 1, Fraser, London 1840, S. 275–276.
- ↑ Alfred Lucas, John R. Lucas: Ancient Egyptian Materials and Industries. 4. Auflage. Arnold, London 1962, S. 237.
- ↑ a b c Verein Deutscher Eisenhüttenleute: Gemeinfassliche Darstellung des Eisenhüttenwesens. 17. Auflage. Stahleisen, Düsseldorf 1970/71, S. 5.
- ↑ Otto Johannsen: Geschichte des Eisens. 3. Auflage. Stahleisen, Düsseldorf 1953, ISBN 3-514-00002-6, S. 45.
- ↑ Sophus Müller: Eisenzeit. Walter de Gruyter GmbH & Co KG, 2019, ISBN 978-3-11-144101-6, S. 9 (eingeschränkte Vorschau in der Google-Buchsuche).
- ↑ Legenden: 2000 Jahre Varusschlacht Geschichte – Archäologie – Legenden. Walter de Gruyter, 2012, ISBN 978-3-11-028251-1, S. 154 (eingeschränkte Vorschau in der Google-Buchsuche).
- ↑ Erik Myrstener, William Lidberg, Ulf Segerström, Harald Biester, David Damell, Richard Bindler: Was Moshyttan the earliest iron blast furnace in Sweden? The sediment record as an archeological toolbox. In: Journal of Archaeological Science: Reports. Band 5, 2016, S. 35–44. doi:10.1016/j.jasrep.2015.10.040.
- ↑ Norbert Welsch, Jürgen Schwab, Claus Liebmann: Materie. Springer Berlin Heidelberg, 2013, S. 255 (eingeschränkte Vorschau in der Google-Buchsuche).
- ↑ a b c Hans Berns, Werner Theisen: Eisenwerkstoffe – Stahl und Gusseisen. Springer-Verlag, 2008, ISBN 978-3-540-79957-3, S. 396 (eingeschränkte Vorschau in der Google-Buchsuche).
- ↑ Klaus Urban: Materialwissenschaft und Werkstofftechnik Ein Ritt auf der Rasierklinge. Springer-Verlag, 2015, ISBN 978-3-662-46237-9, S. 28 (eingeschränkte Vorschau in der Google-Buchsuche).
- ↑ Berg- und hüttenmännische Zeitung: N.F. 50. (1896). Deutschland: Felix. eingeschränkte Vorschau in der Google-Buchsuche
- ↑ a b Mineralienatlas:Mineralienportrait/Eisen.
- ↑ Chad Brand, Charles W. Draper, Archie England: Holman Illustrated Bible Dictionary. B&H Publishing Group, 2015, ISBN 978-0-8054-9935-3, S. 162 (eingeschränkte Vorschau in der Google-Buchsuche).
- ↑ Bernhard Neumann: Die Metalle. Рипол Классик, 1904, ISBN 5-87731-632-X, S. 8 (eingeschränkte Vorschau in der Google-Buchsuche).
- ↑ David Stronach: Metal Objects from the 1957 Excavations at Nimrud. In: Iraq. Band 20, 1958, S. 169–181, doi:10.2307/4199639.
- ↑ Richard Kieffer, Werner Hotop: Sintereisen und Sinterstahl. Springer-Verlag, 2013, ISBN 978-3-7091-3951-6, S. 4 (eingeschränkte Vorschau in der Google-Buchsuche).
- ↑ Otto Johannsen: Geschichte des Eisens. 3. Auflage. Stahleisen, Düsseldorf 1953, ISBN 3-514-00002-6, S. 9–11.
- ↑ Mineralienatlas Lexikon: Eisen, abgerufen am 5. Januar 2023.
- ↑ J. C. Carr, W. Taplin: History of the British Steel Industry. Basil Blackwell, Oxford 1962, ISBN 978-0-631-07100-6, S. 1: “… the industry’s growing demand for fuel had so depleted timber reserves … as to create a serious national problem.”
- ↑ Detlev Forst, Maximilian Kolb, Helmut Roßwag: Chemie für Ingenieure. Springer Berlin Heidelberg, 2013, ISBN 978-3-662-00654-2, S. 235 (eingeschränkte Vorschau in der Google-Buchsuche).
- ↑ Franz Fischer, Hans Tropsch: Über die Herstellung synthetischer Ölgemische (Synthol) durch Aufbau aus Kohlenoxyd und Wasserstoff. In: Brennstoff-Chem. 4, 1923, S. 276–285.
- ↑ Franz Kainer: Die Kohlenwasserstoff-Synthese nach Fischer-Tropsch. Springer Berlin Heidelberg, 1950, ISBN 3-642-49125-1, S. 16 (eingeschränkte Vorschau in der Google-Buchsuche).
- ↑ a b c U.S. Geological Survey, Mineral Commodity Summaries 2022: IRON,STEEL.
- ↑ Bundesministerium für Wirtschaft und Klimaschutz: BMWK – Stahlindustrie, abgerufen am 22. Januar 2023.
- ↑ DERA Rohstoffinformationen 17: Ursachen von Preispeaks, -einbrüchen und -trends bei mineralischen Rohstoffen »Auftragsstudie« (PDF, 9 MB) (2013), abgerufen am 23. Januar 2023.
- ↑ IKB: Information Rohstoffpreise, KW 27, 5. Juli 2022, abgerufen am 23. Januar 2023.
- ↑ a b Stig R. Johansson: On the History of Fire Tools and Matches. Intermatch Sweden AB, Jönköping/Pyroteknikdagen 1983, S. 5 (englisch).
- ↑ Martin Bertau, Armin Müller, Peter Fröhlich, Michael Katzberg, Karl Heinz Büchel, Hans-Heinrich Moretto, Dietmar Werner: Industrielle Anorganische Chemie. Wiley, 2013, ISBN 978-3-527-64958-7, S. 715 (eingeschränkte Vorschau in der Google-Buchsuche).
- ↑ Claudia Preiser: Achilleus’ Heilmittel für Telephos in den "kyprien", in Euripides’ "telephos", bei Plinius und bei Apollodor. In: Rheinisches Museum für Philologie. Band 144, Nr. 3/4, 2001, S. 277–286, JSTOR:41234501.
- ↑ Gesellschaft Deutscher Chemiker: Chemie der Elemente, Mai 2019, abgerufen am 6. Januar 2023.
- ↑ Ingo Klöckl: Grundlagen, Pigmente und Farbmittel. Walter de Gruyter GmbH & Co KG, 2020, ISBN 978-3-11-064915-4, S. 276 (eingeschränkte Vorschau in der Google-Buchsuche).
- ↑ Hugo Schwanert: Lehrbuch der pharmaceutischen Chemie. Schwetschke, 1883, S. 672 (eingeschränkte Vorschau in der Google-Buchsuche).
- ↑ Georg Schwedt: Faszinierende chemische Experimente. Wiley, 2019, ISBN 978-3-527-82203-4, S. 30 (eingeschränkte Vorschau in der Google-Buchsuche).
- ↑ Ernst Bartholomé: Ullmanns Encyklopädie der technischen Chemie: Dentalchemie bis Erdölverarbeitung. Verlag Chemie, 1975, ISBN 3-527-20000-2, S. 411 (eingeschränkte Vorschau in der Google-Buchsuche).
- ↑ Gérard Jaouen, Nils Metzler-Nolte, Roger Alberto: Medicinal Organometallic Chemistry. Springer, 2010, ISBN 978-3-642-13184-4, S. 82 (eingeschränkte Vorschau in der Google-Buchsuche).
- ↑ Katharina Lodders: Solar System Abundances of the Elements. In: Principles and Perspectives in Cosmochemistry. 2010, S. 379–417. Crossref. Web.
- ↑ J. Theo Kloprogge, Concepcion P. Ponce, Tom Loomis: The Periodic Table: Nature's Building Blocks. Elsevier Science, 2020, ISBN 978-0-12-821538-8, S. 351 (eingeschränkte Vorschau in der Google-Buchsuche).
- ↑ Hannu Karttunen, Pekka Kröger, Heikki Oja, Markku Poutanen, Karl Johan Donner: Fundamental Astronomy. 5. Auflage. Springer, Berlin / Heidelberg / New York 2007, ISBN 978-3-540-34143-7, 10.3 Stellar Energy Sources, S. 237 (englisch, finnisch: Tähtitieteen perusteet. Helsinki 2003.).
- ↑ Mathias Scholz: Die Physik der Sterne Aufbau, Entwicklung und Eigenschaften. Springer-Verlag, 2018, ISBN 978-3-662-57801-8, S. 500 (eingeschränkte Vorschau in der Google-Buchsuche).
- ↑ Katia Moskvitch: Neutron Stars. Harvard University Press, 2020, ISBN 978-0-674-91935-8, S. 137 (eingeschränkte Vorschau in der Google-Buchsuche).
- ↑ Steckbrief: Die Sonne – unser Zentralgestirn. In: Spektrum.de. Spektrum der Wissenschaft Verlagsgesellschaft mbH, 2014-09-06, abgerufen am 2. Januar 2023.
- ↑ Mathias Scholz: Planetologie extrasolarer Planeten. Springer, Berlin/Heidelberg 2014, ISBN 978-3-642-41749-8, S. 269 (eingeschränkte Vorschau in der Google-Buchsuche).
- ↑ Renee C. Weber, Pei-Ying Lin, Edward J. Garnero, Quentin Williams, Philippe Lognonné: Seismic Detection of the Lunar Core. In: Science. Band 331, 2011, S. 309–312, doi:10.1126/science.1199375 (Volltext (PDF) ( vom 15. Oktober 2015 im Internet Archive)).
- ↑ Stuart Ross Taylor: Lunar science: A post-Apollo view. Pergamon Press, New York 1975, S. 64 (online).
- ↑ Claude Allègre, Gérard Manhès, Éric Lewin: Chemical composition of the Earth and the volatility control on planetary genetics. In: Earth and Planetary Science Letters. Band 185, 2001, S. 49–69; doi:10.1016/S0012-821X(00)00359-9.
- ↑ David R. Lide (Hrsg.): CRC Handbook of Chemistry and Physics. 85. Auflage. CRC Press, Boca Raton, Florida, 2005. Section 14, Geophysics, Astronomy, and Acoustics; Abundance of Elements in the Earth's Crust and in the Sea.
- ↑ William M. Haynes: CRC Handbook of Chemistry and Physics. 92. Auflage. Taylor & Francis, 2011, ISBN 978-1-4398-5511-9 (hbcpnetbase.com).
- ↑ John Grotzinger, Thomas Jordan: Press/Siever Allgemeine Geologie. Springer-Verlag, 2016, ISBN 978-3-662-48342-8, S. 11 (eingeschränkte Vorschau in der Google-Buchsuche).
- ↑ Werner Gocht: Handbuch der Metallmärkte Erzvorkommen, Metallgewinnung, Metallverwendung Preisbildung Handelsregelungen. Springer-Verlag, 2013, ISBN 978-3-642-86964-8, S. 31 (eingeschränkte Vorschau in der Google-Buchsuche).
- ↑ Slobodan Jankovic: Wirtschaftsgeologie der Erze. Springer-Verlag, 2013, ISBN 978-3-7091-5100-6, S. 96 (eingeschränkte Vorschau in der Google-Buchsuche).
- ↑ Gregor Markl: Minerale und Gesteine Mineralogie – Petrologie – Geochemie. Springer-Verlag, 2014, ISBN 978-3-662-44628-7 (eingeschränkte Vorschau in der Google-Buchsuche).
- ↑ Walter Kölle: Wasseranalysen – richtig beurteilt Grundlagen, Parameter, Wassertypen, Inhaltsstoffe, Grenzwerte nach Trinkwasserverordnung und EU-Trinkwasserrichtlinie. John Wiley & Sons, 2012, ISBN 978-3-527-65984-5, S. 84 (eingeschränkte Vorschau in der Google-Buchsuche).
- ↑ Lexikon der Geowissenschaften: Banded Iron Formation, abgerufen am 5. Oktober 2019.
- ↑ a b c Martin Bertau, Armin Müller, Peter Fröhlich, Michael Katzberg: Industrielle Anorganische Chemie. John Wiley & Sons, 2013, ISBN 978-3-527-33019-5, S. 696, 252 (eingeschränkte Vorschau in der Google-Buchsuche).
- ↑ Ellen Morris Bishop, John Eliot Allen: Hiking Oregon's geology. Mountaineers, 1996, S. 200 (eingeschränkte Vorschau in der Google-Buchsuche).
- ↑ Walter Hähnel, Werner Buggisch, Christian Buggisch: Mineralien und Gesteine. TESSLOFF Verlag, 1994, ISBN 3-7886-2850-2, S. 35 (eingeschränkte Vorschau in der Google-Buchsuche).
- ↑ F. J. Berry: Chemical Bonding and Spectroscopy in Mineral Chemistry. Springer Science & Business Media, 2012, ISBN 978-94-009-4838-9, S. 92 (eingeschränkte Vorschau in der Google-Buchsuche).
- ↑ Martin Okrusch, Siegfried Matthes: Mineralogie Eine Einführung in die spezielle Mineralogie, Petrologie und Lagerstättenkunde. Springer-Verlag, 2010, ISBN 978-3-540-78201-8, S. 70 (eingeschränkte Vorschau in der Google-Buchsuche).
- ↑ Rudolf Winderlich: Lehrbuch der Chemie für Höhere Lehranstalten Einheitsausgabe für Unter- und Oberstufe. Springer-Verlag, 2013, ISBN 978-3-663-04370-6, S. 75 (eingeschränkte Vorschau in der Google-Buchsuche).
- ↑ Jenny Feige: Astronomie unter dem Meer: Spuren des Isotops 60 Fe weisen auf nahe Supernovae hin. In: Physik in unserer Zeit. Band 47, Nr. 5, 2016, S. 220–227, doi:10.1002/piuz.201601446.
- ↑ Eisenisotope zur Datierung, abgerufen am 4. Dezember 2022
- ↑ Geology for Investors: Iron Deposits – Banded Iron Formations (BIF) | Geology for Investors, abgerufen am 7. Oktober 2019.
- ↑ Iron. In: John W. Anthony, Richard A. Bideaux, Kenneth W. Bladh, Monte C. Nichols (Hrsg.): Handbook of Mineralogy, Mineralogical Society of America. 2001 (englisch, handbookofmineralogy.org [PDF; 46 kB; abgerufen am 3. September 2024]).
- ↑ Localities for Iron. In: mindat.org. Hudson Institute of Mineralogy, abgerufen am 3. September 2024 (englisch).
- ↑ Malcolm Back, Cristian Biagioni, William D. Birch, Michel Blondieau, Hans-Peter Boja und andere: The New IMA List of Minerals – A Work in Progress – Updated: July 2024. (PDF; 3,6 MB) In: cnmnc.units.it. IMA/CNMNC, Marco Pasero, Juli 2024, abgerufen am 3. September 2024 (englisch).
- ↑ Laurence N. Warr: IMA–CNMNC approved mineral symbols. In: Mineralogical Magazine. Band 85, 2021, S. 291–320, doi:10.1180/mgm.2021.43 (englisch, cambridge.org [PDF; 351 kB; abgerufen am 3. September 2024]).
- ↑ Ernest H. Nickel, Monte C. Nichols: IMA/CNMNC List of Minerals 2009. (PDF; 1,9 MB) In: cnmnc.units.it. IMA/CNMNC, Januar 2009, archiviert vom (nicht mehr online verfügbar) am 29. Juli 2024; abgerufen am 30. Juli 2024 (englisch).
- ↑ William Jervis Jones: Historisches Lexikon deutscher Farbbezeichnungen. Band 1. Akademie Verlag, Berlin 2013, ISBN 978-3-05-005953-2, S. 835 (eingeschränkte Vorschau in der Google-Buchsuche).
- ↑ Stefan Weiß: Das große Lapis Mineralienverzeichnis. Alle Mineralien von A – Z und ihre Eigenschaften. Stand 03/2018. 7., vollkommen neu bearbeitete und ergänzte Auflage. Weise, München 2018, ISBN 978-3-921656-83-9.
- ↑ Josephinit. In: Mineralienatlas Lexikon. Geolitho Stiftung, abgerufen am 1. April 2023.
- ↑ David Barthelmy: Mineral Species sorted by the element Fe (Iron). In: webmineral.com. Abgerufen am 3. September 2024 (englisch).
- ↑ a b c d e f g h i j W. Ternes: Biochemie der Elemente: Anorganische Chemie biologischer Prozesse. Springer-Verlag, 2012, ISBN 978-3-8274-3020-5, S. 108,127 (eingeschränkte Vorschau in der Google-Buchsuche).
- ↑ a b Iron Ore Statistics and Information: Iron Ore Statistics and Information 2019, abgerufen am 8. Oktober 2019.
- ↑ United States Geological Survey: World Production (PDF; 298 kB).
- ↑ World Steel in Figures 2020. (PDF) World Steel Association, archiviert vom (nicht mehr online verfügbar) am 3. Juli 2020; abgerufen am 3. Juli 2020 (englisch).
- ↑ Fact sheet – Steel and raw materials. (PDF) In: worldsteel.org. Abgerufen am 14. März 2023 (englisch).
- ↑ Luossavaara-Kiirunavaara AB: Mining, abgerufen am 9. Oktober 2019.
- ↑ Günther Schwemmer: Die Geschichte der Eisengewinnung in der mittleren Oberpfalz im 19. und 20. Jahrhundert. diplom.de, 2001, ISBN 3-8324-4262-6, S. 129 (eingeschränkte Vorschau in der Google-Buchsuche).
- ↑ Der Fischer Weltalmanach 2001. Fischer Taschenbuch Verlag, 2000, ISBN 978-3-596-72001-9, S. 1157 (eingeschränkte Vorschau in der Google-Buchsuche).
- ↑ a b c Heinz M. Hiersig: VDI-Lexikon Maschinenbau. Springer-Verlag, 2013, ISBN 978-3-642-57850-2, S. 520 (eingeschränkte Vorschau in der Google-Buchsuche).
- ↑ a b H. Berns, L. Scheer: Was ist Stahl – Eine Stahlkunde für jedermann. Springer-Verlag, 2013, ISBN 978-3-642-61846-8, S. 100 (eingeschränkte Vorschau in der Google-Buchsuche).
- ↑ a b Wolfgang Bleck, Elvira Moeller: Handbuch Stahl Auswahl, Verarbeitung, Anwendung. Carl Hanser Verlag GmbH Co KG, 2017, ISBN 978-3-446-44962-6, S. 78,386 (eingeschränkte Vorschau in der Google-Buchsuche).
- ↑ Helmut Veil: Wasserrad, Dampfmaschine, Holzkohle, Koks und Eisen. Humanities Online, 2022, ISBN 978-3-941743-90-8, S. 70 (eingeschränkte Vorschau in der Google-Buchsuche).
- ↑ Heinz-Gerhard Franck, Andre Knop: Kohleveredlung. Springer Berlin Heidelberg, 2013, ISBN 978-3-540-09627-6, S. 98 (eingeschränkte Vorschau in der Google-Buchsuche).
- ↑ Energieverbrauch und CO2-Emissionen industrieller Prozesstechnologien – Einsparpotenziale, Hemmnisse und Instrumente. In: fraunhofer.de. Fraunhofer Bookshop, abgerufen am 6. Februar 2023.
- ↑ Lösch, Oliver & Prof. Dr. Jochem, Eberhard & Ashley-Belbin, Natalia & Zesch, Gregor. (2020). Bewertung der Direktreduktion von Eisenerz mittels Elektrolyse-Wasserstoff.
- ↑ Heinz Brauer (Hrsg.): Handbuch des Umweltschutzes und der Umweltschutztechnik Band 2: Produktions- und produktintegrierter Umweltschutz. Springer-Verlag, 2013, ISBN 978-3-642-60943-5, S. 340 (eingeschränkte Vorschau in der Google-Buchsuche).
- ↑ M. Shamsuddin: Physical Chemistry of Metallurgical Processes. John Wiley & Sons, 2016, ISBN 978-1-119-07833-3, S. 237 (eingeschränkte Vorschau in der Google-Buchsuche).
- ↑ Ludwig von Bogdandy, H.-J. Engell: Die Reduktion der Eisenerze Wissenschaftliche Grundlagen und technische Durchführung. Springer-Verlag, 2013, ISBN 978-3-642-92935-9, S. 33 (eingeschränkte Vorschau in der Google-Buchsuche).
- ↑ Christoph Meyer: Operative Planung des Recyclings von Eisenhüttenschlacken. Springer Fachmedien Wiesbaden, 2019, ISBN 978-3-658-26239-6, S. 8 (eingeschränkte Vorschau in der Google-Buchsuche).
- ↑ Otto Henning: Baustoffchemie Eine Einführung für Bauingenieure und Architekten. Beuth Verlag, 2013, ISBN 978-3-410-22481-5, S. 53 (eingeschränkte Vorschau in der Google-Buchsuche).
- ↑ Simone Franke: Giesserei-Lexikon 2019. Schiele & Schoen, 2019, ISBN 978-3-7949-0916-2, S. 181 (eingeschränkte Vorschau in der Google-Buchsuche).
- ↑ Jürgen Ruge: Technologie der Werkstoffe für Studenten des Maschinenbaus und der Verfahrenstechnik ab 1. Semester. Springer-Verlag, 2013, ISBN 978-3-322-84025-7, S. 75 (eingeschränkte Vorschau in der Google-Buchsuche).
- ↑ John Wright: Environmental Chemistry. Taylor & Francis, 2004, ISBN 1-134-58965-4, S. 127 (eingeschränkte Vorschau in der Google-Buchsuche).
- ↑ Verein Deutscher Eisenhüttenleute: Gemeinfassliche Darstellung des Eisenhüttenwesens. 17. Auflage. Stahleisen, Düsseldorf 1970/71, S. 103–118.
- ↑ a b c d Amit Chatterjee: Beyond the Blast Furnace. CRC Press, 2017, ISBN 978-1-351-46424-6, S. 128 (eingeschränkte Vorschau in der Google-Buchsuche).
- ↑ Hans Bodo Lüngen, Peter Schmöle: History, developments and processes of direct reduction of iron ores, Presented at the 8th European Coke and Ironmaking Congress and the 9 th International Conference on Science and Technology of Ironmaking in Bremen, Germany, 29. August bis 2. September 2022, abgerufen am 18. Februar 2023.
- ↑ Bewertung der Direktreduktion von Eisenerz mittels Elektrolyse-Wasserstoff, Studie im Rahmen des Vorhabens EE4lnG: Energieeffizienz für Industrie und Gewerbe, IREES GmbH, abgerufen am 18. Februar 2023.
- ↑ a b Can Yilmaz: Maßnahmen zur Dekarbonisierung des Hochofenprozesses durch Einsatz von Wasserstoff. Cuvillier Verlag, 2018, S. 82 (eingeschränkte Vorschau in der Google-Buchsuche).
- ↑ Hermann Schenck: Reduktion von Eisenerzen mit Öl und Erdgas. VS Verlag für Sozialwissenschaften, 2013, S. 12 (eingeschränkte Vorschau in der Google-Buchsuche).
- ↑ a b c d e Hermann Sicius: Eisengruppe: Elemente der achten Nebengruppe Eine Reise durch das Periodensystem. Springer-Verlag, 2016, ISBN 978-3-658-15561-2, S. 20,22 (eingeschränkte Vorschau in der Google-Buchsuche).
- ↑ Arabinda Sarangi, Bidyapati Sarangi: Alternative Routes to Iron Making. Prentice Hall India Pvt., Limited, 2016, ISBN 978-81-203-5119-6, S. 256 (eingeschränkte Vorschau in der Google-Buchsuche).
- ↑ Ernest Arthur Boas: Die eisenschaffende Industrie Brasiliens. Duncker & Humblot, 1957, ISBN 3-428-00208-3, S. 106 (eingeschränkte Vorschau in der Google-Buchsuche).
- ↑ Direktreduktion: Diese Technik wird bei Thyssenkrupp und Co. den Hochofen beerben, VDI nachrichten, abgerufen am 18. Februar 2023.
- ↑ a b A. F. Holleman, E. Wiberg, N. Wiberg: Lehrbuch der Anorganischen Chemie. 102. Auflage. Walter de Gruyter, Berlin 2007, ISBN 978-3-11-017770-1, S. 1334.
- ↑ Martin Bertau, Armin Müller, Peter Fröhlich, Michael Katzberg, Karl Heinz Büchel, Hans-Heinrich Moretto, Dietmar Werner: Industrielle Anorganische Chemie. John Wiley & Sons, 2013, ISBN 978-3-527-64958-7, S. 252 (eingeschränkte Vorschau in der Google-Buchsuche).
- ↑ B. E. Hopkins: The Preparation and Properties of High-Purity Iron. In: Metallurgical Reviews. Band 1, Nr. 1, 1956, S. 117–155, doi:10.1179/mtlr.1956.1.1.117.
- ↑ Michael F. Ashby, Hugh Shercliff, David Cebon: Materials. Elsevier Science, 2013, ISBN 978-0-08-099435-2, S. 597-IA35 (eingeschränkte Vorschau in der Google-Buchsuche).
- ↑ a b A. E. van Arkel, K. Lins: Reine Metalle. Springer Berlin Heidelberg, 1939, S. 312 (eingeschränkte Vorschau in der Google-Buchsuche).
- ↑ W. Pepperhoff, M. Acet: Konstitution und Magnetismus des Eisens und seiner Legierungen. Springer, Berlin, Heidelberg 2000, ISBN 3-642-59765-3, Struktur des Eisens, S. 1–14, doi:10.1007/978-3-642-59765-7_1.
- ↑ M. P. Fewell: The atomic nuclide with the highest mean binding energy. In: American Journal of Physics. Band 63, Nr. 7, 1995, S. 653–658, doi:10.1119/1.17828 (englisch).
- ↑ G. Audi, O. Bersillon, J. Blachot, A. H. Wapstra: The NUBASE evaluation of nuclear and decay properties. In: Nuclear Physics. Band A 729, 2003, S. 3–128. doi:10.1016/j.nuclphysa.2003.11.001. (PDF; 1,0 MB).
- ↑ a b François Cardarelli: Materials Handbook A Concise Desktop Reference. Springer Science & Business Media, 2008, ISBN 978-1-84628-669-8, S. 65 (eingeschränkte Vorschau in der Google-Buchsuche).
- ↑ Ping Hu, Ning Ma, Li-zhong Liu, Yi-guo Zhu: Theories, Methods and Numerical Technology of Sheet Metal Cold and Hot Form... Springer London, 2012, ISBN 978-1-4471-4099-3, S. 79 (eingeschränkte Vorschau in der Google-Buchsuche).
- ↑ Reinhard Boehler: High-pressure experiments and the phase diagram of lower mantle and core materials. In: Reviews of Geophysics. Band 38. American Geophysical Union, 2000, S. 221–245, doi:10.1029/1998RG000053.
- ↑ Tateno, S. Hirose, K.: The Structure of Iron in Earth's Inner Core. In: Science. 330. Jahrgang, Nr. 6002. American Association for the Advancement of Science, 2010, S. 359–361, doi:10.1126/science.1194662, PMID 20947762, bibcode:2010Sci...330..359T.
- ↑ Gaminchev Chamati: Dynamic stability of Fe under high pressure. In: Journal of Physics. 558. Jahrgang, Nr. 1. IOP Publishing, 2014, S. 012013, doi:10.1088/1742-6596/558/1/012013, bibcode:2014JPhCS.558a2013G.
- ↑ Reinhard Boehler, M. Ross: Mineral Physics. Hrsg.: Elsevier (= Treatise on Geophysics. Band 2). 2007, Properties of Rocks and Minerals – High-Pressure Melting, S. 527–541.
- ↑ Die chemische Zusammensetzung unentwickelter Sterne der Spektraltypen A und F. S. 32, 55 (eingeschränkte Vorschau in der Google-Buchsuche).
- ↑ Lexikon der Astronomie: Eisenlinie – Lexikon der Astronomie, abgerufen am 11. Februar 2018.
- ↑ Charles Steinmetz: Theory and Calculation of Electric Circuits. Hrsg.: McGraw-Hill. 1917, Fig. 42.
- ↑ a b c Hans Berns, Werner Theisen: Eisenwerkstoffe Stahl Und Gusseisen. Springer-Verlag, 2012, ISBN 978-3-642-31923-5, S. 118 (eingeschränkte Vorschau in der Google-Buchsuche).
- ↑ a b B. D. Cullity, C. D. Graham: Introduction to Magnetic Materials, 2nd. Wiley–IEEE, New York 2008, ISBN 978-0-471-47741-9, S. 116 (google.com).
- ↑ Greenwood and Earnshaw, S. 1075–1079.
- ↑ B. L. Bramfitt, Arlan O. Benscoter: Metallographer's guide: practice and procedures for irons and steels. ASM International, 2002, ISBN 0-87170-748-9, The Iron Carbon Phase Diagram, S. 24–28 (eingeschränkte Vorschau in der Google-Buchsuche).
- ↑ H. Schmitz, W. Jäniche: Werkstoffkunde Stahl. Springer, Berlin, Heidelberg 1984, ISBN 3-642-82091-3, S. 443 (eingeschränkte Vorschau in der Google-Buchsuche).
- ↑ a b Wissenschaft-Online-Lexika: Eintrag zu Eisen im Lexikon der Chemie, abgerufen am 14. November 2019.
- ↑ Alfred Böge (Hrsg.): Das Techniker-Handbuch. 13., überarbeitete Auflage. Vieweg, Braunschweig 1992, ISBN 3-528-14053-4, S. 523.
- ↑ a b c Eintrag zu Eisen. In: Römpp Online. Georg Thieme Verlag, abgerufen am 26. Mai 2014.
- ↑ D. Glindemann, A. Dietrich, H.-J. Staerk, P. Kuschk: Die zwei Gerüche des Eisens bei Berührung und unter Säureeinwirkung – (Haut)Carbonylverbindungen und Organophosphine. In: Angewandte Chemie. Band 118, Nr. 42, 2006, S. 7163–7166 (doi:10.1002/ange.200602100).
- ↑ a b c d Wolfgang Mücke, Christa Lemmen: Duft und Geruch Wirkungen und gesundheitliche Bedeutung von Geruchsstoffen. ecomed-Storck GmbH, 2010, ISBN 978-3-609-16436-6, S. 76 (eingeschränkte Vorschau in der Google-Buchsuche).
- ↑ G. Audi, F. G. Kondev, Meng Wang, W.J. Huang, S. Naimi: The NUBASE2016 evaluation of nuclear properties. In: Chinese Physics C. 41, 2017, S. 030001, doi:10.1088/1674-1137/41/3/030001 (Volltext)
- ↑ Anna Schuh-Renner, Adam Fritsch, M. Heim, A. Shore, M. Thoennessen: Discovery of the Iron Isotopes. In: Atomic Data and Nuclear Data Tables. Band 96, 2010, S. 817–823. doi:10.1016/j.adt.2010.06.003.
- ↑ Alan P. Dickin: Radiogenic Isotope Geology. Cambridge University Press, 2018, ISBN 978-1-107-09944-9, S. 422 (eingeschränkte Vorschau in der Google-Buchsuche).
- ↑ Heinrich D. Holland, Karl K. Turekian: Radioactive Geochronometry A derivative of the Treatise on Geochemistry. Academic Press, 2010, ISBN 978-0-08-096708-0, S. 50 (eingeschränkte Vorschau in der Google-Buchsuche).
- ↑ Harry Y. McSween, Jr, Gary R. Huss: Cosmochemistry. Cambridge University Press, 2010, ISBN 978-1-139-48946-1, S. 290 (eingeschränkte Vorschau in der Google-Buchsuche).
- ↑ Nadja Podbregar: Supernova schuld an Massenaussterben? In: scinexx.de. 23. Dezember 2018, abgerufen am 6. März 2024.
- ↑ Gero Vogl: Wandern ohne Ziel Von der Atomdiffusion zur Ausbreitung von Lebewesen und Ideen. Springer-Verlag, 2007, ISBN 978-3-540-71064-6, S. 86 (eingeschränkte Vorschau in der Google-Buchsuche).
- ↑ a b Karl H. Koch: Industrielle Prozeßanalytik. Springer-Verlag, 2013, ISBN 978-3-662-01083-9, S. 102 (eingeschränkte Vorschau in der Google-Buchsuche).
- ↑ Stephan Hasse: Gefüge der Gusseisenlegierungen. Fachverlag Schiele & Schoen, 2007, S. 55 (eingeschränkte Vorschau in der Google-Buchsuche).
- ↑ Erwin Riedel, Hans-Jürgen Meyer: Allgemeine und Anorganische Chemie. Walter de Gruyter, 2013, ISBN 978-3-11-027013-6, S. 341 (eingeschränkte Vorschau in der Google-Buchsuche).
- ↑ a b Karl A. Hofmann: Anorganische Chemie. Springer-Verlag, 2013, ISBN 978-3-663-14240-9, S. 667 (eingeschränkte Vorschau in der Google-Buchsuche).
- ↑ Erhard Hornbogen, Hans Warlimont: Metallkunde Aufbau und Eigenschaften von Metallen und Legierungen. Springer-Verlag, 2013, ISBN 978-3-662-08697-1, S. 292 (eingeschränkte Vorschau in der Google-Buchsuche).
- ↑ Franz Zach: Leistungselektronik Ein Handbuch Band 1 /. Springer-Verlag, 2015, ISBN 978-3-658-04899-0, S. 1828 (eingeschränkte Vorschau in der Google-Buchsuche).
- ↑ Aaron Foisi Nmungwun: Video Recording Technology Its Impact on Media and Home Entertainment. Routledge, 2012, ISBN 978-0-8058-0360-0, S. 38 (eingeschränkte Vorschau in der Google-Buchsuche).
- ↑ Ulrich Schwabe, Dieter Paffrath: Arzneiverordnungs-Report 2016. Springer-Verlag, 2016, ISBN 978-3-662-50351-5, S. 265 (eingeschränkte Vorschau in der Google-Buchsuche).
- ↑ Claus Priesner, Karin Figala (Hrsg.): Alchemie. Lexikon einer hermetischen Wissenschaft. Beck, München 1998, ISBN 3-406-44106-8, S. 123 (Seitenvorschau in der Google-Buchsuche).
- ↑ Helmut Plattner, Joachim Hentschel: Zellbiologie. Georg Thieme Verlag, 2006, ISBN 3-13-106513-3, S. 277 (eingeschränkte Vorschau in der Google-Buchsuche).
- ↑ Harold Zeliger: Oxidative Stress. Elsevier Science, 2022, ISBN 978-0-323-91458-1, S. 215 (eingeschränkte Vorschau in der Google-Buchsuche).
- ↑ Ludger Rensing, Volkhard Rippe: Altern. Springer Berlin Heidelberg, 2013, ISBN 978-3-642-37733-4, S. 25 (eingeschränkte Vorschau in der Google-Buchsuche).
- ↑ Eintrag zu Ferritin. In: Römpp Online. Georg Thieme Verlag, abgerufen am 26. Mai 2014.
- ↑ F. Widdel, S. Schnell, S. Heising, A. Ehrenreich, B. Assmus, B. Schink: Ferrous iron oxidation by anoxygenic phototrophic bacteria. In: Nature. Vol. 362, 1993, S. 834–836; Abstract.
- ↑ Klaus Schümann, Thomas Ettle, Bernadett Szegner, Bernd Elsenhans, Noel W. Solomons: Risiken und Nutzen der Eisensupplementation: Empfehlungen zur Eisenaufnahme kritisch betrachtet. In: Perspectives in Medicine. Band 2, Nr. 1, 2014, S. 19–39, doi:10.1016/j.permed.2013.09.003.
- ↑ Eberhard J. Wormer: Eisen. Kopp Verlag, 2016, ISBN 978-3-86445-324-3 (eingeschränkte Vorschau in der Google-Buchsuche).
- ↑ Cem Ekmekcioglu, Wolfgang Marktl: Essentielle Spurenelemente. Springer, 2006, ISBN 3-211-20859-3, S. 8 (eingeschränkte Vorschau in der Google-Buchsuche).
- ↑ Y. Kohgo, K. Ikuta, T. Ohtake, Y. Torimoto, J. Kato: Body iron metabolism and pathophysiology of iron overload. In: International Journal of Hematology. Band 88, Nummer 1, Juli 2008, S. 7–15, doi:10.1007/s12185-008-0120-5. PMID 18594779. PMC 2516548 (freier Volltext).
- ↑ M. Auerbach, H. Ballard: Clinical use of intravenous iron: administration, efficacy, and safety. In: Hematology / the Education Program of the American Society of Hematology. American Society of Hematology. Education Program. 2010, S. 338–347, doi:10.1182/asheducation-2010.1.338. PMID 21239816.
- ↑ J. M. McDermid, B. Lönnerdal: Iron. In: Advances in nutrition (Bethesda, Md.). Band 3, Nummer 4, Juli 2012, S. 532–533, doi:10.3945/an.112.002261. PMID 22797989. PMC 3649722 (freier Volltext).
- ↑ U. E. Schaible, S. H. Kaufmann: Iron and microbial infection. In: Nat. Rev. Microbiol. Band 2, Nr. 12, Dezember 2004, S. 946–953, doi:10.1038/nrmicro1046, PMID 15550940.
- ↑ Medizin – Kommunikation: DEGUM: Parkinson-Erkrankung vor dem Ausbruch erkennen. Arbeitsgemeinschaft der Wissenschaftlichen Medizinischen Fachgesellschaften, Pressemitteilung vom 6. Juli 2006 beim Informationsdienst Wissenschaft (idw-online.de), abgerufen am 20. Dezember 2014.
- ↑ Fragen und Antworten zu Eisen in Lebensmitteln – BfR. Abgerufen am 26. Februar 2024.
- ↑ Günter Fellenberg: Chemie der Umweltbelastung. 3. Auflage. Verlag B. G. Teubner, Stuttgart 1997, ISBN 3-519-23510-2, S. 158.
- ↑ Barbara Grüttner, Wilhelm Fresenius, H. Hahn, Gerhart Jander: Elemente der Achten Nebengruppe Eisen · Kobalt · Nickel. Springer-Verlag, 2013, ISBN 978-3-662-36753-7, S. 128 (eingeschränkte Vorschau in der Google-Buchsuche).
- ↑ Edward Lyons: Thioglycolic Acid as a Color Test for Iron. In: Journal of the American Chemical Society. Band 49, Nr. 8, 1927, S. 1916–1920, doi:10.1021/ja01407a010.
- ↑ A. F. Holleman, E. Wiberg, N. Wiberg: Lehrbuch der Anorganischen Chemie. 102. Auflage. Walter de Gruyter, Berlin 2007, ISBN 978-3-11-017770-1, S. 1650.
- ↑ Gerhart Jander, Ewald Blasius: Lehrbuch der analytischen und präparativen anorganischen Chemie. 12. Auflage. S. Hirzel Verlag, Stuttgart 1983, ISBN 3-7776-0379-1, S. 221.
- ↑ Ehlers, Eberhard: Analytik, Bd.1, Kurzlehrbuch Qualitative pharmazeutische Analytik. Deutscher Apotheker Verlag, 2001, ISBN 3-7692-2710-7, S. 320.
- ↑ a b c E. Schweda: Jander/Blasius: Anorganische Chemie I – Einführung & Qualitative Analyse. 17. Auflage. Hirzel, Stuttgart 2012, ISBN 978-3-7776-2134-0, S. 337.
- ↑ Jun-Bo Lu, Jiwen Jian, Wei Huang, Hailu Lin, Jun Li, Mingfei Zhou: Experimental and theoretical identification of the Fe(VII) oxidation state in FeO4−. In: Physical Chemistry Chemical Physics. Band 18, Nr. 45, 2016, S. 31125–31131, doi:10.1039/C6CP06753K.
- ↑ Chemie für Ingenieure. Pearson Deutschland, 2008, ISBN 978-3-8273-7267-3, S. 256 (eingeschränkte Vorschau in der Google-Buchsuche).
- ↑ Detlef Schroeder, Andreas Fiedler u. a.: Generation and Characterization of the Anionic, Neutral, and Cationic Iron-Dioxygen Adducts [FeO2] in the Gas Phase. In: Inorganic Chemistry. Band 33, 1994, S. 5094, doi:10.1021/ic00100a039.
- ↑ Georg Brauer (Hrsg.) u. a.: Handbuch der Präparativen Anorganischen Chemie. 3., umgearbeitete Auflage. Band III, Ferdinand Enke, Stuttgart 1981, ISBN 3-432-87823-0, S. 1648.
- ↑ Patent DE60002011T2: Verfahren zur Herstellung einer wässrigen Eisen(III)-Sulfat-Lösung und ihre Verwendung als Wasserbehandlungsreagenz. Angemeldet am 20. Juni 2000, veröffentlicht am 29. Januar 2004, Anmelder: Taki Chemical Co. Ltd, Erfinder: Toshihiko Kakio, Tatsuo Tsukamoto.
- ↑ ColourLex: Prussian Blue, abgerufen am 20. März 2023.